What is Flux and How Does It Work in Soldering?
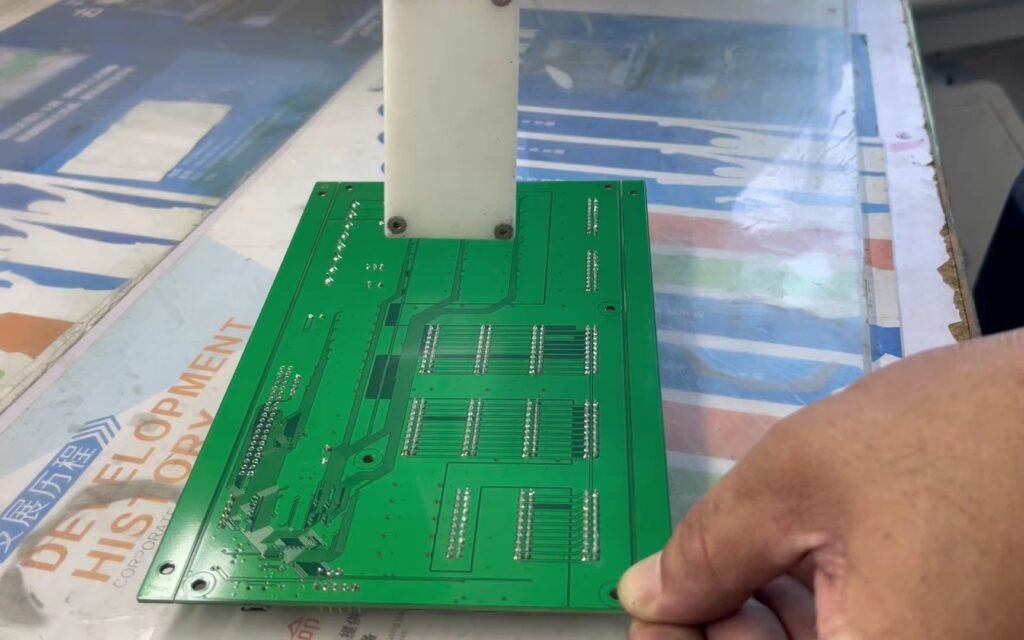
Soldering is a critical process in electronics manufacturing that involves connecting electronic components to printed circuit boards (PCBs). To achieve a reliable and robust connection, a specialized chemical agent known as flux is used. But what exactly is flux, and what role does it play in the soldering process?
In simple terms, flux is a powerful cleaning agent used to remove impurities and oxides from the metal surfaces of PCBs and component leads before soldering. This step is essential for ensuring strong solder joints and preventing corrosion between the metals.
Without proper flux cleaning, solder won't adhere correctly to the components or the PCB, leading to weak and unreliable joints. However, selecting the right type of flux and applying it properly is equally important for ensuring high-quality, durable solder connections.
The Role of Flux in Soldering
Flux plays a vital role in the formation of solder joints. During the soldering process, metal impurities may be present on the PCB or the components, which can interfere with proper solder flow. Flux is used to clean the surface of these impurities and remove any oxidation from the exposed metal surfaces, ensuring a clean and uniform connection.
Once the flux has cleaned the surface, it prepares the area for a strong, high-integrity solder joint. However, after soldering, the remaining flux residue must be removed as part of the final cleaning process. The method of cleaning depends on the type of flux used.
Flux is a mixture of active chemicals and base materials. It functions as an activator, removing oxides from metal surfaces and promoting better wetting of the solder. Depending on the final application, different types of flux may lead to more successful manufacturing outcomes.
Types of Flux and Application Methods
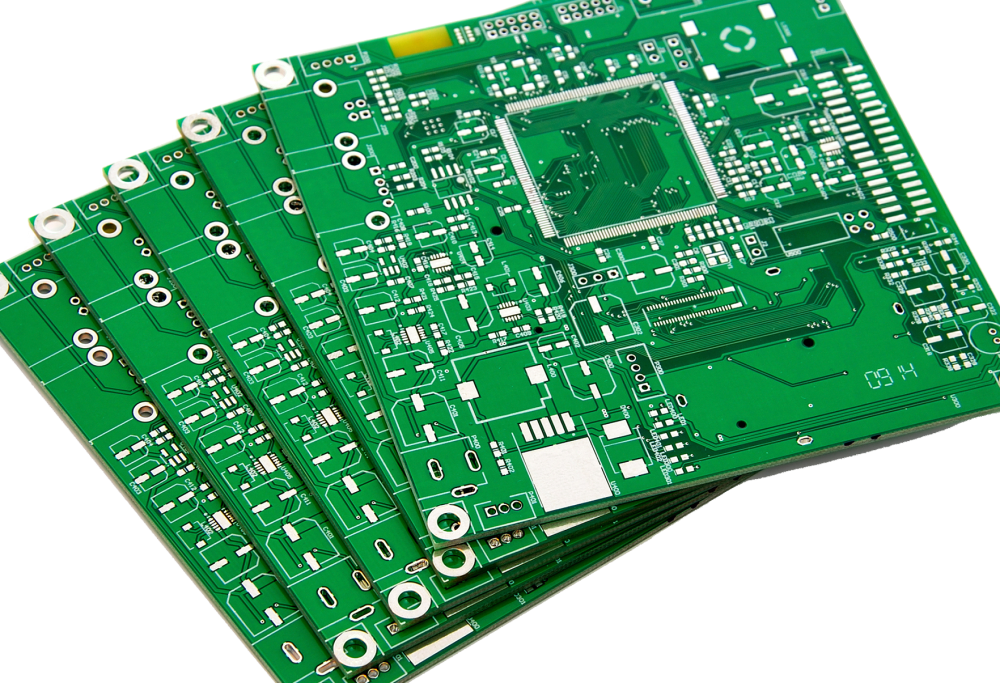
Flux is typically applied in one of the following ways, each suited to different soldering processes. The choice of flux type and application method depends on the specific requirements of the component and the PCB being soldered.
1. Wave Soldering
In wave soldering, flux is applied to the PCB before it passes through a wave of molten solder. The flux composition includes various solvents that clean the PCB’s surface and remove oxides from the components. Depending on the manufacturing process, the PCB may need to be pre-cleaned before applying flux.
2. Solder Reflow
In reflow soldering, solder paste, which contains flux, is printed onto the PCB in areas where components are to be soldered. The components are placed on the solder paste, and the assembly is heated in a reflow oven. The flux in the paste helps clean the metal surfaces while also preventing further oxidation. As the solder paste melts, it forms a solid bond between the component leads and the PCB pads.
3. Selective Soldering
In selective soldering, flux is applied precisely to the areas of the PCB that require soldering. This can be done via spraying or dispensing to target specific areas, ensuring that the rest of the PCB remains free from flux.
Cleaning Flux Residues
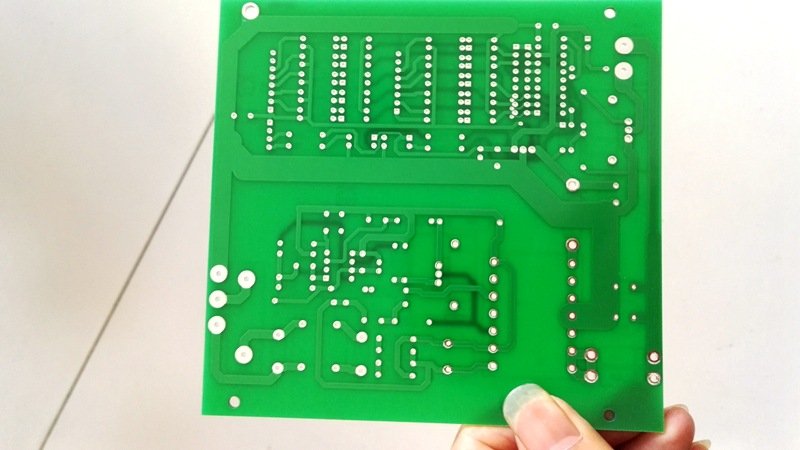
Flux is corrosive and can adversely affect the PCB's performance if left behind. It's important to thoroughly clean the PCB after soldering to avoid long-term degradation.
Flux comes in three main types, each with different cleaning requirements:
1. Rosin-Based Flux
This type of flux is widely used in electronic soldering and requires specific chemical solvents to remove residual flux. These solvents usually contain fluorocarbon compounds. However, many countries now have strict regulations on the use and disposal of these chemicals, leading to a preference for more eco-friendly alternatives.
2. Water-Soluble Flux
Water-soluble flux is easier to clean than other types, using deionized water or mild detergents for removal. This option is considered more environmentally friendly, as it does not require harsh chemicals for cleaning.
3. No-Clean Flux
As the name suggests, no-clean flux leaves very little residue and requires minimal post-soldering cleaning. While the flux residue doesn't usually affect the performance of the PCB, it can cause issues with sensitive electronic and optical detection equipment. For this reason, cleaning is still recommended, even though it’s not always necessary to prevent defects.
Choosing the Right Flux for Your Application
The type of flux you choose depends on the specific application, customer requirements, and the complexity of the component layout. Working closely with your contract manufacturer (CM) during the design phase can help you identify the most appropriate flux manufacturing process for your solution.
At CustomPCBA, we offer no-clean and water-soluble flux options to support your soldering process. Our team works closely with clients to ensure the best possible flux selection based on the needs of their electronic assemblies, while adhering to stringent quality and environmental standards.
By understanding the critical role that flux plays in soldering, you can ensure your PCBs have high-quality solder joints that meet the demanding performance standards of modern electronic devices.
Is Flux Necessary for Soldering?
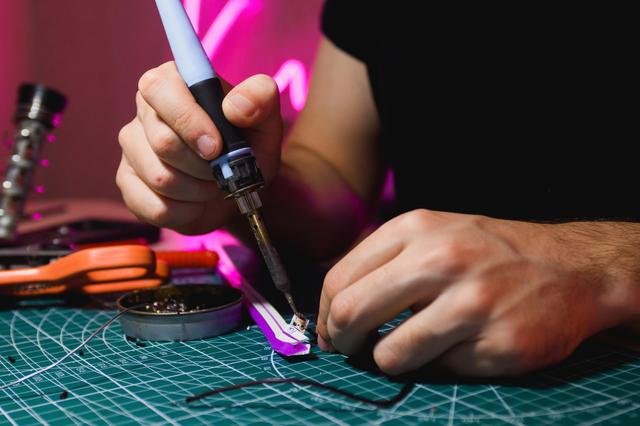
The answer is a resounding yes—flux is absolutely essential for effective soldering. It plays a crucial role in cleaning the surfaces of the metals being joined by removing oxides and impurities, thus ensuring the formation of clean, reliable solder joints. These contaminants can hinder the solder's ability to properly wet the surface, leading to weak or unreliable connections.
From a professional manufacturing standpoint, the use of flux becomes even more critical. Clean and strong solder joints are vital for the long-term reliability of the product, and flux is instrumental in achieving that. Furthermore, certain types of soldering, such as surface-mount soldering and reflow soldering, require the application of flux due to the precision involved in these processes.
For individuals working on small batches or hand-soldering circuit boards, flux significantly enhances the accuracy of the soldering process, resulting in more durable and reliable electrical connections. It is particularly useful when dealing with older components or those that have higher levels of oxidation, as flux helps remove this oxidation and ensure a solid connection.
What is Flux Made From?
Flux is primarily made from rosin, a natural resin obtained from pine tree sap. However, manufacturers often blend rosin with other chemicals to enhance its effectiveness. These additives may include activators such as acids or amine halides, which improve the flux's ability to remove oxidation from metal surfaces. In some formulations, solvents are also added to make the flux easier to apply and spread across the surfaces being soldered.
Professional-grade flux typically incorporates more complex chemical mixtures that are optimized for specific soldering conditions. These specialized fluxes are designed to meet strict industry standards, such as those set by the IPC (Institute for Printed Circuits), ensuring consistent performance across various manufacturing environments. Additionally, flux formulations are tailored to address specific challenges in high-precision processes or demanding applications, such as aerospace or medical electronics.
Can Flux Degrade Over Time?
While flux generally has a long shelf life, it can degrade over time, especially if not stored properly. Exposure to high temperatures, light, or moisture can accelerate this degradation, compromising its effectiveness when applied during soldering.
It is essential to follow the manufacturer's guidelines regarding storage conditions and expiration dates to ensure optimal performance. For environments where large volumes of flux are used regularly, maintaining proper storage conditions becomes critical not only to avoid wastage but also to preserve the flux's quality and functionality.
For individual users, it's important to note that opened containers of flux are more vulnerable to degradation due to exposure to air. Regularly replacing flux and ensuring that containers are sealed tightly when not in use will help maintain the quality and performance of the flux, ensuring consistent soldering results.
Flux Types and Their Applications
There are several types of flux available, each suited to different soldering applications. The choice of flux type depends on the specific requirements of the assembly, including the nature of the components and the soldering process involved. Below are some of the most commonly used flux types:
1. Rosin Flux
The most common flux type, often used in general soldering applications. It is effective at cleaning metal surfaces and is widely used in manual soldering, particularly for circuit boards. Rosin flux is typically available in different grades, depending on its purity and the level of activation required for specific tasks.
2. Water-Soluble Flux
Water-soluble fluxes are environmentally friendly and easy to clean using deionized water or mild cleaning agents. These fluxes are often used in applications where easy post-soldering cleaning is necessary, such as in consumer electronics. However, water-soluble flux must be thoroughly cleaned from the PCB to prevent corrosion or long-term degradation.
3. No-Clean Flux
As the name implies, no-clean fluxes are designed to leave minimal residue after soldering, requiring little to no post-soldering cleaning. These fluxes are ideal for applications where cleaning would be difficult or unnecessary, such as in densely populated or highly automated PCBs. While no-clean flux is more convenient in some cases, care must still be taken to ensure that any residue left behind does not interfere with sensitive equipment or testing processes.
Flux Application Methods
Flux can be applied using various techniques, depending on the type of soldering process used and the complexity of the assembly. The most common application methods include:
- Wave Soldering: In wave soldering, flux is applied to the PCB before it enters the wave of molten solder. The flux composition includes solvents that clean the surface and remove any oxides from the component leads and pads.
- Reflow Soldering: During reflow soldering, solder paste, which contains flux, is printed onto the PCB. Components are then placed on the paste and heated in an oven. The flux cleans the surfaces, while the solder paste melts and forms a strong bond between the component and the PCB.
- Selective Soldering: In selective soldering, flux is applied precisely to the required areas of the PCB, typically using spray or precise dispensing methods. This is particularly useful in applications where only certain components need to be soldered.
Conclusion
In summary, flux is a crucial component in the soldering process. It ensures that the metal surfaces are clean, enabling strong and reliable solder joints. Whether you are performing hand-soldering, reflow soldering, or wave soldering, flux plays an indispensable role in achieving high-quality, durable solder connections. By understanding the different types of flux, their composition, and how to apply them, manufacturers and technicians can improve soldering results and avoid common pitfalls like weak joints or long-term corrosion.
For professional-grade, high-quality flux solutions, CustomPCBA offers a range of flux types, including no-clean and water-soluble options, to meet the specific needs of your assembly. By choosing the right flux and adhering to proper storage and application methods, you can ensure optimal soldering performance in any electronic manufacturing environment.