PCB etching is a crucial step in the manufacturing of printed circuit boards (PCBs), involving the precise removal of copper from the PCB surface to reveal the desired circuit patterns. This process is vital for creating the electrical pathways that allow devices to function.
During PCB etching, copper is selectively removed from the board, except for areas protected by tin plating. Once the etching is complete, the tin is stripped away, leaving behind a clean copper surface with the precise design intended for the circuit.
Though the concept may seem straightforward, the PCB etching process is quite intricate and demands high levels of accuracy. Several etching methods are available, each offering distinct advantages and challenges.
In this guide, we will dive deeper into the PCB etching process, its importance in PCB manufacturing, and how we at [Your Company Name] ensure that your etching needs are met with the utmost precision. Whether you’re looking for custom PCB solutions or aiming to understand the intricacies of the etching process, this article provides a comprehensive overview.
What is PCB Etching?
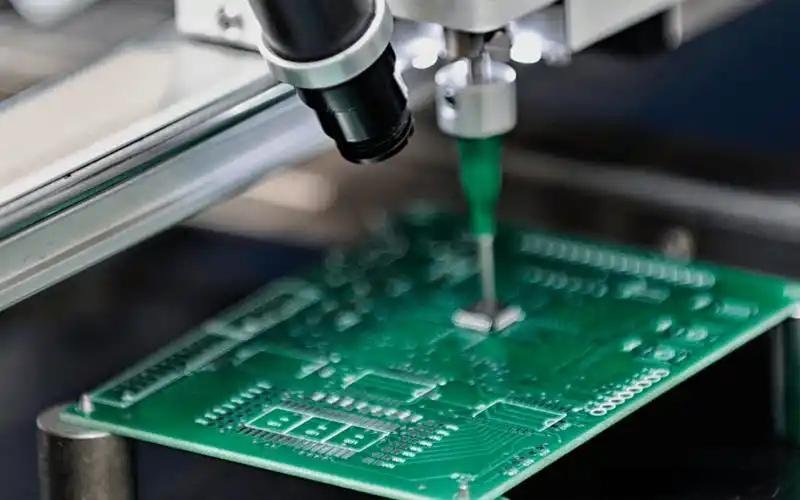
PCB etching is a critical process in the manufacturing of printed circuit boards (PCBs) where excess copper is removed from the surface of the board to reveal the desired circuit pattern. This process is essential in forming the conductive paths that allow electrical signals to travel across the PCB, enabling it to perform its intended function in electronic devices.
Before the etching process begins, a layout design of the PCB circuit is created. Using a photolithographic process, the circuit pattern is transferred onto the PCB, essentially serving as a blueprint for the areas where copper will remain and where it will be etched away.
In this process, the outer layers of the PCB are protected by a layer of tin plating, which acts as a resist. For inner layers, photoresist is used as a protective coating. The etching process can be carried out using two primary techniques: dry etching and wet etching, each with its own set of advantages and limitations.
At [Custompcba], we use Tech Win alkaline etching machines for the wet etching process, ensuring precision and efficiency.
Dry Etching
Dry etching is a more advanced technique that uses plasma to activate chemical reactions between the atoms of the substrate and the surface atoms. This results in the dissolution of the unwanted copper, leaving behind the desired circuit design. Although plasma is typically employed in dry etching, lasers can also be used for this purpose.
Plasma Etching
Plasma etching has been in use since the 1960s and became more popular in the 1970s. This method was developed to reduce the liquid waste involved in traditional wet etching processes while also providing greater selectivity in areas that wet chemical processes could not achieve as easily.
In plasma etching, a glow discharge (plasma) of appropriately mixed gases is directed at the PCB, causing unwanted copper to dissolve without the need for chemicals. This dry, clean process offers high precision and controlled etching within a very small area. Additionally, plasma etching significantly reduces the risk of contamination in vias and prevents solvents from being absorbed into the board.
However, plasma etching is expensive and may not be cost-effective unless large volumes of etching are required.
Laser Etching
Laser etching uses precise computer-controlled hardware to direct high-power lasers onto the PCB substrate, engraving the desired patterns by vaporizing or peeling off unwanted copper. One of the major benefits of laser etching is its ability to eliminate multiple process steps, especially the need for ink, acids, or toxic chemicals.
Laser etching is highly precise and can produce intricate features on the PCB. However, it may struggle with uniform etching on larger boards, and residual copper or etching agents can be challenging to remove. Like plasma etching, laser etching tends to be expensive and more suitable for smaller, specialized runs rather than mass production.
Wet Etching
Wet etching involves the use of a chemical solution to dissolve unwanted copper from the PCB. Depending on the etching material, either acidic or alkaline chemicals can be used to achieve the desired result.
Acidic Etching
Acidic etching is commonly used for etching the inner layers of rigid PCBs. Copper chloride or ferric chloride are typically used in this process. Copper chloride is especially favored because it offers precise etching of fine features, consistent etching rates, and continuous regeneration.
Acidic etching is especially effective on inner layers because the acid does not react with the photoresist, protecting the desired parts of the board. Additionally, undercutting—the lateral etching of the copper beneath the solder mask—is minimized in acidic etching. However, acidic etching tends to be slower and more time-consuming than alkaline etching, making it less suited for mass production.
Alkaline Etching
Alkaline etching is widely used for etching the outer layers of PCBs, and it is the method employed by [Your Company Name] for most of our PCB manufacturing processes. This approach is fast, cost-efficient, and well-suited for high-volume production.
However, the alkaline etching process requires strict control to avoid overexposure of the PCB to the etching solution, which can lead to damage. The process is often performed in a high-pressure spray chamber where the PCB is exposed to a mist of fresh etching solution, ensuring rapid, consistent results.
During the etching process, unwanted copper is dissolved, and the exposed copper features form the etched circuits. The process reaches a point where the excess copper is fully etched away, resulting in a clean, functional PCB.
PCB etching is an essential step in the creation of printed circuit boards, with several methods available to achieve the precise removal of copper. Whether using dry etching techniques like plasma or laser, or wet etching methods like acid and alkaline etching, precision and control are key to ensuring the performance and reliability of the final product. At [Your Company Name], we utilize the best technologies and processes to ensure that your PCBs meet the highest quality standards. Contact us today to learn more about our PCB etching capabilities and how we can support your project.
How Our PCB Etching Machine Works
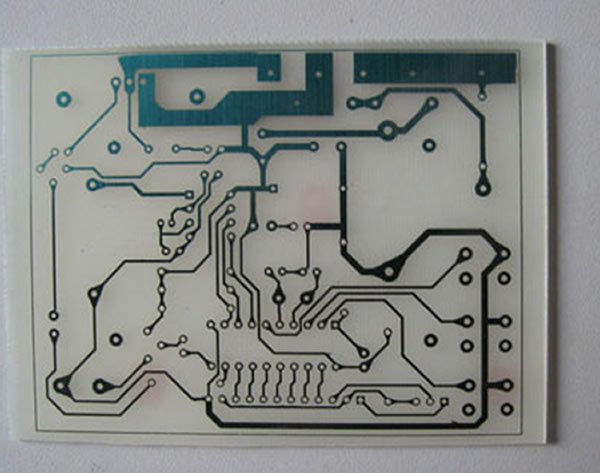
In the world of PCB manufacturing, there are various types of etching machines available, each using different techniques such as lasers or plasma to remove unwanted materials from the surface of the PCB. However, at [Your Company Name], we utilize the advanced Amonicon Edge Solution with our Tech Win Alkaline Etching Machine to achieve highly precise and efficient results.
During the PCB manufacturing process, specifically at the etching stage, the PCB is carefully placed on a conveyor belt inside our Tech Win etching machine. Once activated, the conveyor belt starts to move, gradually pulling the PCB into the machine’s etching chamber.
Inside the chamber, the PCB is sprayed with Amonicon Edge Solution, a specially formulated chemical solution that plays a crucial role in removing unwanted copper from the PCB. The solution is designed to etch away all exposed copper areas not protected by a tin coating, leaving only the areas that have been covered by the solder mask.
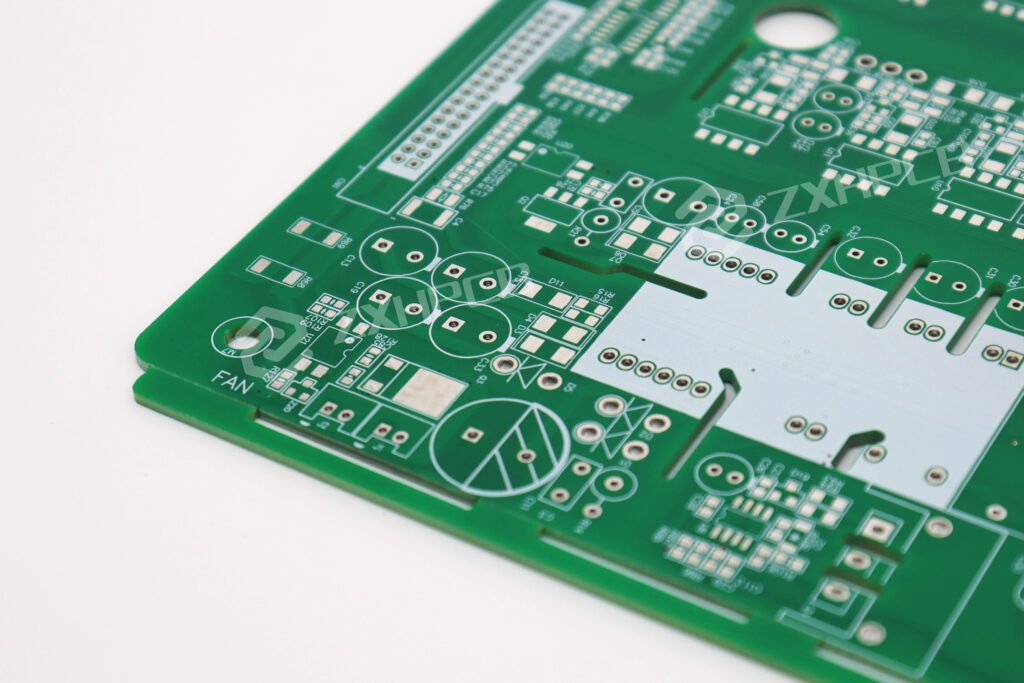
The result is a clean, etched pattern of copper traces that form the conductive pathways across the PCB. These copper traces, also known as etch lines, are essential for creating the electrical connections that allow current and voltage to flow throughout the circuit. These traces link the components on the PCB, enabling them to interact and function as intended within the device.
Our etching process is carefully controlled to ensure precision at every step, which is critical to producing high-quality PCBs that meet the stringent performance requirements of modern electronic devices. By using Amonicon Edge Solution, we can ensure that the etching is uniform, minimizing undercutting and ensuring the integrity of fine features and traces.
In summary, our PCB etching machine uses a precise and controlled process to selectively remove unwanted copper, leaving behind the exact circuit pattern needed to create functional and reliable PCBs. This process ensures that the final product can efficiently conduct electrical signals and support the performance of the devices it powers.
How to Get Started with CustomPCBA?
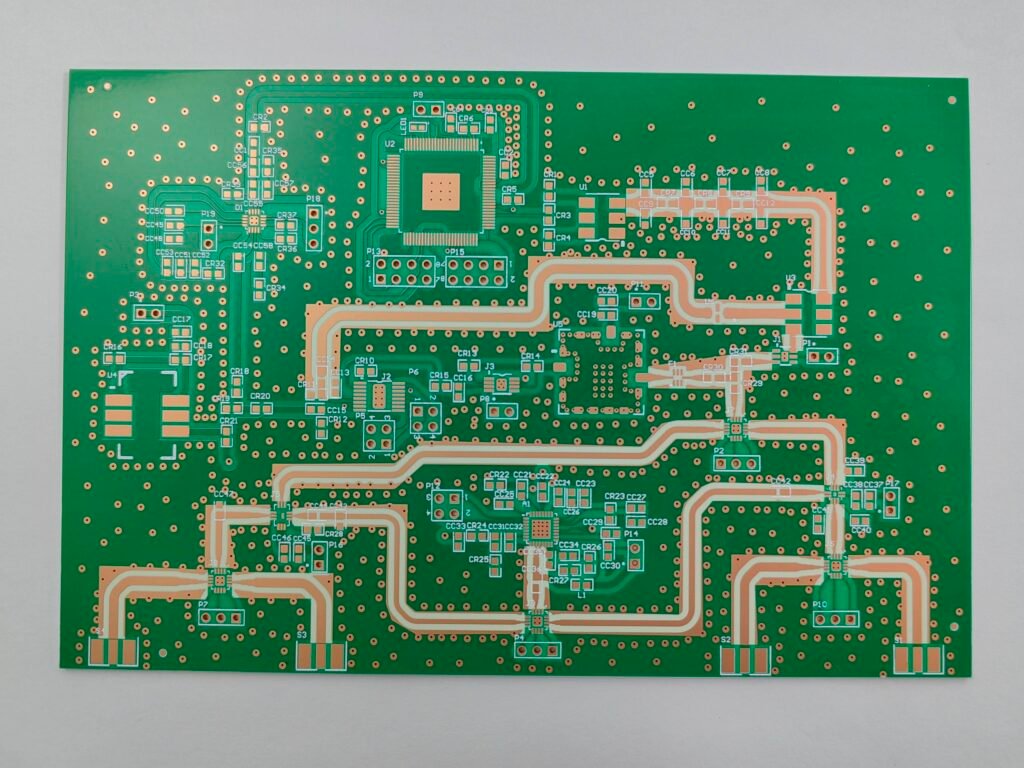
CustomPCBA is a leading PCB manufacturer offering high-quality printed circuit board solutions for industries across the board. Whether you need custom manufacturing, design services, or PCB prototyping, we bring nearly 40 years of professional expertise to deliver tailored PCB solutions that meet all your needs.
Getting started with us is simple. Just fill out our contact form, and one of our technical experts will reach out to you promptly to provide timely, professional support. You can also contact us directly via email at long@custompcba.com, and we will be happy to assist you.
By partnering with CustomPCBA, you’ll enjoy industry-leading lead times and efficient service. We prioritize client privacy and data security, always adhering to strict confidentiality agreements, ensuring a worry-free service experience. Our customer base includes long-term partners who trust us to develop proprietary circuits under strict confidentiality and provide innovative solutions.
We take great pride in delivering perfection on every project and are confident in offering tailored, precise PCB solutions for every client. Our customer satisfaction guarantee reflects our commitment to quality, and our skilled technical team’s meticulous attention to detail ensures exceptional results.
Get a Free Custom Quote Today!
Ready to get started? Request a completely free, no-obligation quote from our expert team today. If you already know the type of PCB services you require, please provide as much detail as possible so we can better understand your needs and offer the most suitable solution.
Whether you need PCB design, manufacturing, or assembly, we’re here to help you with expert guidance and ensure your project is completed successfully.