In the production of nearly all electronic devices, solder plays a crucial role in connecting components to the printed circuit board (PCB). While lead-based solder was once the industry standard for assembling these boards, manufacturers have gradually shifted away from using lead, opting for safer alternatives in everything from industrial machinery to consumer electronics.
Solder comes in various forms, with the best choice depending on the specific application. Today, lead-free soldering is the most widely adopted method for PCB assembly in electronic products.
This article will delve into the differences between lead-based and lead-free solder, discussing the environmental and health benefits of eliminating this toxic and hazardous element from the manufacturing process.
What is Solder?
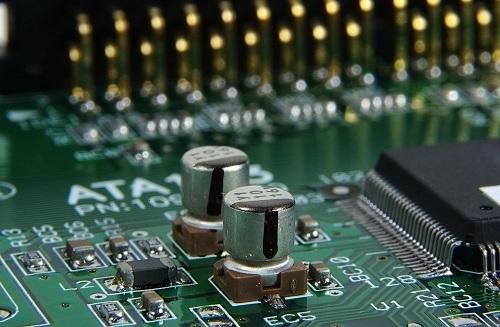
Solder is a metal alloy used to connect electronic components to a printed circuit board (PCB). Its primary function is to create a reliable electrical and mechanical connection by melting and solidifying between two metal surfaces. Various types of solder are used depending on the metals being joined, and the choice of solder is based on several factors, such as:
- Form: Solder comes in different forms, including wire, paste, or pellets.
- Core Style: Solder can contain different fluxes, such as rosin core or acid core, to help the solder flow and bond effectively.
- Working Temperature: The melting point of solder must be lower than the melting point of the metals it is joining.
The basic soldering process involves placing components onto a PCB, heating the joint, and applying the solder to create the bond. Once the solder cools, the joint solidifies, and excess leads are trimmed.
The two primary types of solder used in electronics assembly are lead-based solder and lead-free solder. While lead-based solder was once the standard, lead-free solder has become the preferred choice due to health and environmental concerns.
Leaded vs. Lead-Free Solder
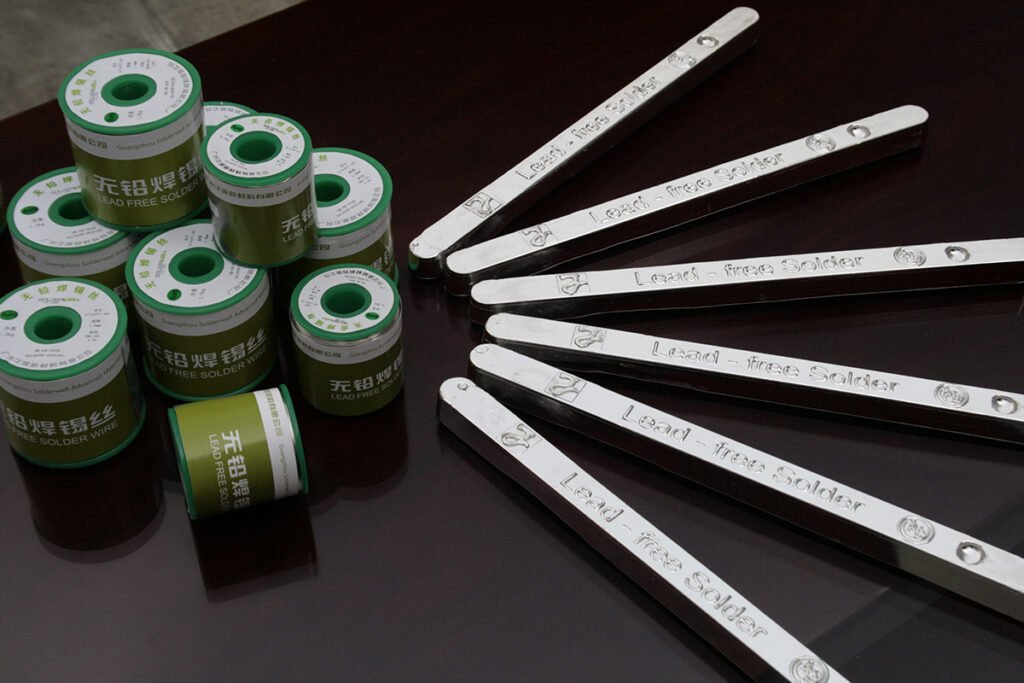
Characteristics of Leaded Solder
Leaded solder (SnPb) is a metal alloy primarily composed of tin (Sn) and lead (Pb). This type of solder was favored in electronics assembly for several reasons:
- Slower Cooling: Leaded solder cools more slowly than other solder alloys, reducing the risk of cracking in the joint.
- Effective Wetting: It provides excellent wetting properties, creating strong electrical connections between leads and PCB pads.
- Lower Melting Point: Leaded solder has a lower and well-defined melting point compared to other alloys, making it easier to work with and less likely to damage delicate components.
However, leaded solder has significant drawbacks due to lead’s toxicity. Lead exposure is known to cause serious health issues, including cognitive impairment and developmental problems, especially in children. This has led to increasing regulations restricting the use of lead in electronic products.
Characteristics of Lead-Free Solder
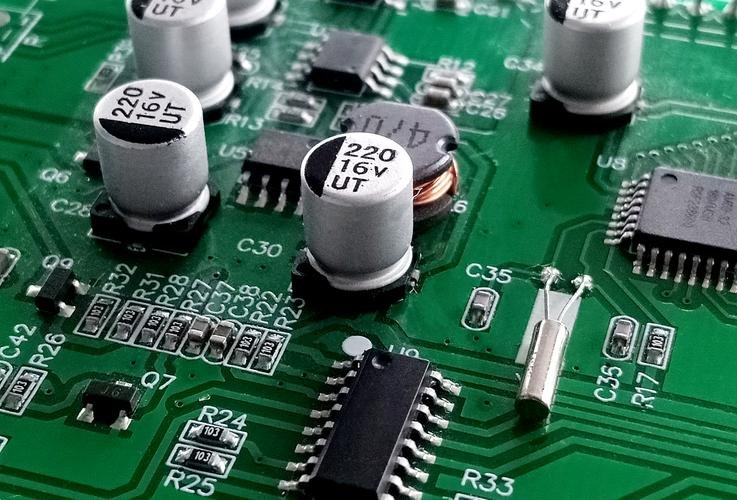
Lead-free solder is a metal alloy that typically consists of various combinations of tin, copper, silver, and other metals. The most common lead-free alloy contains tin (Sn) and copper (Cu), though other formulations may include elements like silver (Ag), bismuth (Bi), or nickel (Ni). Lead-free solder has the following characteristics:
- Higher Melting Point: Lead-free solders generally have higher melting points than leaded solders, which means they require higher temperatures to melt. This makes soldering more challenging, but it is not typically a problem in modern electronics assembly.
- Stronger Bonds: Lead-free solder creates stronger and harder joints, which is beneficial for the mechanical integrity of electronic devices.
- Environmental Benefits: Lead-free solder reduces the risk of environmental contamination, especially given the widespread disposal of electronic waste.
Lead-free solder is widely adopted in most electronic applications, but it may not be suitable for specific high-stress applications like aerospace or medical devices, where additional mechanical strength is required.
Key Benefits of Lead-Free Solder
- Healthier for Workers and Consumers
The most significant advantage of using lead-free solder is the improved health and safety of workers and consumers. Lead exposure can cause short-term issues such as fatigue, headaches, and abdominal pain, as well as long-term damage to the nervous system, kidneys, and reproductive organs. By avoiding lead-based solder, manufacturers reduce the risks associated with occupational exposure, while consumers benefit from safer, non-toxic products. - Environmental Protection
Lead is a highly toxic metal that can cause severe environmental damage. It can contaminate air, soil, and water when electronic waste is improperly disposed of. Lead particles can be absorbed by plants and enter the food chain. By using lead-free solder, manufacturers help reduce the environmental impact of their products, especially as the volume of electronic waste continues to rise globally. - Better for PCB Soldering
Lead-free alloys are generally better suited for PCB assembly, especially when it comes to reflow soldering. Unlike lead-based solder, which can create voids or cause joints to lift, lead-free solder flows more effectively and results in stronger, more durable connections. This makes it ideal for consumer electronics, where long-term reliability is critical. - Compliance with Regulations
Many countries and regions have introduced regulations that prohibit the use of lead in consumer electronics. For example, the European Union’s RoHS (Restriction of Hazardous Substances) directive bans the use of lead in electrical and electronic equipment. The United States and China also have regulations that encourage or mandate the use of lead-free solder. Using lead-free solder helps manufacturers meet these regulations and ensures their products can be sold in global markets. - Compatibility with Existing Manufacturing Processes
One of the key benefits of lead-free solder is that it is compatible with existing manufacturing processes. While lead-free solder requires slightly higher temperatures to melt, most PCB manufacturers have adapted their equipment to handle these requirements. As a result, switching from lead-based solder to lead-free solder is relatively easy and does not require major changes to the production line.
Conclusion
As environmental concerns and health risks associated with lead exposure continue to grow, lead-free solder has become the preferred choice for most modern electronics assembly. Although lead-free solder has a higher melting point and slightly different handling characteristics, its environmental, health, and performance advantages outweigh these challenges. For manufacturers, adopting lead-free solder is not only a regulatory requirement in many regions but also a critical step in ensuring the sustainability and safety of their products in today’s global market.