PCB Applications in the Automotive Industry
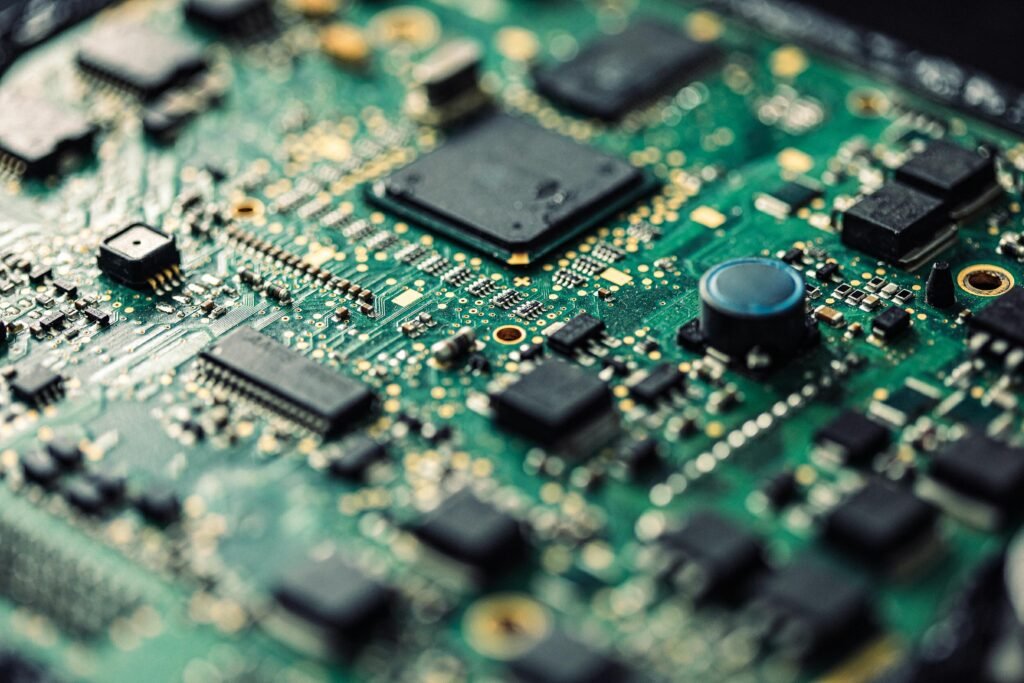
The automotive industry is undergoing a transformative shift, driven by the need for reduced emissions, the development of electric and autonomous vehicles, and the expansion of charging infrastructure. These changes present both exciting opportunities and complex challenges. At MCL, we are committed to driving innovation in the automotive sector, providing advanced PCB solutions tailored to meet the evolving needs of the industry. These applications play a critical role in shaping the future of automotive technology and sustainability.
1. Electric Vehicle Charging Systems
Electric vehicle (EV) charging systems require high-power transmission to ensure efficient and safe charging. For precise control of high-power transfer, PCBs used in charging stations must handle high current while managing heat effectively. These applications demand robust functionality, large copper cross-sections, and superior thermal management capabilities.
- Technical Requirements: High-power transmission, current-carrying capability, excellent thermal management
- Common Designs: HDI (High-Density Interconnect), Multilayer, Thick Copper
- Applications: Charging station control boards, power module PCBs
2. Electric Vehicle Propulsion Systems
Electric vehicle propulsion systems are central to the performance of electric drivetrains, involving motor control, battery management, power distribution, motion control, and cooling systems. These PCBs must operate reliably under harsh conditions, supporting high current and heat dissipation while ensuring long-term durability.
- Technical Requirements: High reliability, large copper cross-section, thermal management, ISO/IATF16949, PPAP quality assurance
- Common Designs: HDI, Multilayer
- Applications: Battery Management Systems (BMS), motor drive control boards
3. Heavy-Duty Vehicle Driver Assistance Systems
Heavy-duty vehicles, including trucks and buses, are increasingly integrating advanced driver assistance systems such as instrument clusters, in-vehicle video systems, navigation, communication modules, and cargo cooling systems. These systems require high-reliability PCBs capable of withstanding extreme environments, such as vibration and fluctuating temperatures.
- Technical Requirements: High reliability, vibration resistance, ISO/IATF16949, PPAP quality assurance
- Common Designs: HDI, Multilayer, Flexible PCBs
- Applications: Instrument clusters, navigation displays, in-vehicle communication modules
4. Fossil-Free Propulsion Systems
As the demand for green transportation solutions increases, fuel cell and battery-powered heavy-duty vehicles are gaining traction. These PCBs must be designed for long-term durability, environmental resistance, and compliance with stringent quality standards to ensure they perform reliably under extreme conditions.
- Technical Requirements: Environmental resistance, long lifespan, compliance with ISO/IATF16949, PPAP quality assurance
- Common Designs: HDI, Multilayer
- Applications: Fuel cell control systems, battery propulsion control systems
5. In-Vehicle Interior Electronics
With the increasing integration of electronic systems in vehicle interiors, technologies like in-vehicle navigation, smart instrument clusters, and ambient lighting are becoming more prevalent. These PCBs must offer high integration, excellent thermal management, and adaptability to complex electronics.
- Technical Requirements: High integration, thermal management, ISO/IATF16949, PPAP quality assurance
- Common Designs: HDI, Multilayer, Flexible PCBs, Rigid-Flex PCBs
- Applications: In-vehicle navigation, instrument clusters, interior lighting control
The Unique Challenges and Advantages of Automotive PCBs
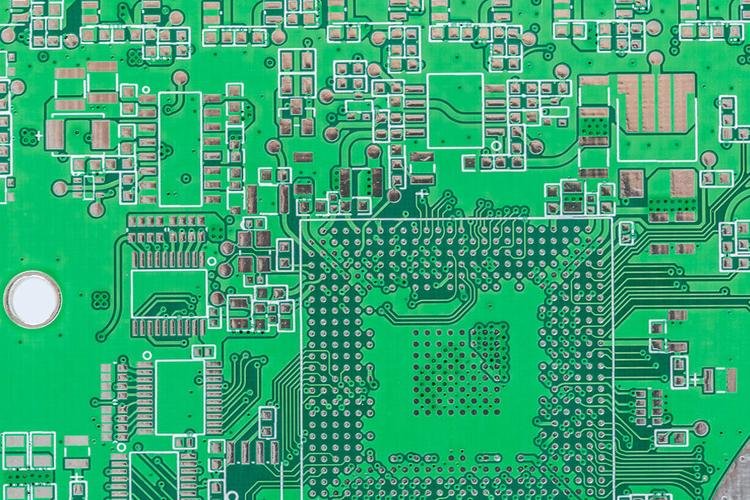
PCBs are integral to modern automotive technology, enabling systems such as engine control, airbag sensors, ABS braking systems, and GPS navigation. With the growing demand for head-up displays, windshield overlays, and other interior electronics, the need for reliable PCBs that do not interfere with other systems is becoming increasingly critical.
Why Choose PCBs:
- High Functionality: PCBs support the integration of complex electronic components and enable a wide range of automotive applications.
- Compact Size: Many automotive electronics require compact PCBs due to limited space, but the small size does not limit functionality. Almost all digital displays you see in a vehicle are controlled by PCBs.
- Reliability: The durability and stability of PCBs make them ideal for long-term use in harsh automotive environments, such as extreme temperatures, vibration, and humidity.
- Ease of Maintenance: Once a PCB is designed, it is easy to replicate and maintain, which helps reduce maintenance costs and time.
Custom Automotive PCB Design: Meeting Your Application Needs
At MCL, we specialize in delivering customized PCB solutions for the automotive industry. With our engineering design and DFM (Design for Manufacturability) support, we can help you achieve high-quality PCBs while optimizing cost efficiency. Our capabilities cover every stage, from prototype design to mass production, ensuring that each product meets the industry's rigorous quality standards.
Our Advantages:
- Highly Customized Design: We tailor PCB designs to meet the specific needs of each customer, ensuring high standards of quality and performance.
- Comprehensive Engineering Support: We provide extensive support throughout the design process, including DFM reviews, thermal analysis, and EMC (Electromagnetic Compatibility) evaluations.
- Strict Quality Management: Our production processes adhere to ISO 9001:2015 standards, and we collaborate with manufacturers who comply with ISO/IATF16949 and PPAP quality assurance systems to ensure reliability and consistency.
- Fast Prototyping: We employ advanced prototyping techniques to quickly produce sample designs and make any necessary adjustments to ensure system support.
- Wide Application Range: Whether for electric vehicles, fuel cells, heavy-duty transportation, or in-vehicle interior electronics, our PCB solutions can support a wide range of automotive innovations.
PCB Applications in Automotive Systems
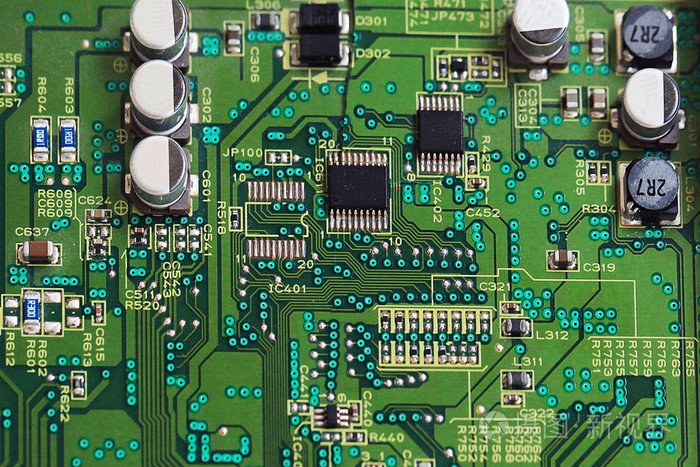
Printed Circuit Boards (PCBs) play an essential role in the automotive industry, enabling the operation of critical safety, control, and entertainment systems. As modern vehicles evolve, the complexity and variety of applications for PCBs continue to expand, offering new opportunities for automotive innovation. From airbags and safety systems to infotainment and power management, automotive PCBs are integrated into almost every aspect of vehicle functionality.
Here’s an in-depth look at some of the key automotive applications for PCBs and how these advanced components are essential to ensuring the safety, reliability, and performance of modern vehicles.
1. Airbag Deployment Systems
One of the most critical applications for PCBs in vehicles is in airbag deployment systems. The airbag system relies on highly reliable sensors and control circuits to detect a collision and trigger the airbag deployment mechanism. These circuits must be able to handle rapid electrical signals, dissipate static charge, and operate within stringent safety tolerances. Therefore, the PCBs in airbag sensors must be designed for high reliability, rapid response times, and robust protection against environmental factors such as temperature and humidity.
- Key Requirements: High reliability, fast response times, electrostatic discharge (ESD) protection
- Applications: Airbag sensors, deployment control units
2. Anti-lock Braking Systems (ABS)
PCBs are also crucial in anti-lock braking systems (ABS), which prevent the wheels from locking during braking, maintaining vehicle control and stability. ABS systems require PCBs to manage sensor data and communicate with the vehicle’s brake control units. These PCBs must handle real-time data processing and ensure safe, precise braking under high-stress conditions, including extreme temperatures and vibrations.
- Key Requirements: Real-time data processing, high vibration resistance, thermal management
- Applications: Brake sensors, control units
3. Infotainment and Audio/Video Systems
Infotainment systems in vehicles, which provide entertainment, navigation, and communication capabilities, are heavily dependent on PCBs. These boards connect and manage the flow of electrical signals between audio/video devices, displays, and communication systems. Automotive PCBs used in infotainment must be designed for high-frequency performance and robust signal integrity, ensuring seamless interaction between devices such as GPS navigation, multimedia systems, and hands-free communication.
- Key Requirements: Signal integrity, high-frequency performance, durability
- Applications: Audio systems, video displays, GPS navigation, communication modules
4. Powertrain Control and Engine Systems
PCBs are integral to the operation of various powertrain components, such as the engine timing system, ignition system, and coolant level monitoring. These systems rely on precise circuit control to ensure that the engine performs efficiently and reliably. For instance, PCBs monitor engine coolant levels, engine performance metrics, and sensor data to regulate the ignition and fuel injection systems, optimizing fuel consumption and minimizing emissions.
- Key Requirements: High current handling, thermal management, signal processing
- Applications: Engine control units (ECUs), ignition systems, fuel injection control, coolant monitoring
5. Power Management and Conversion Systems
Automotive systems, including power converters and electrical distribution, rely on robust PCB designs to convert electrical power for different vehicle components. For example, PCBs in power management systems help regulate battery charging, distribute power to electronic devices, and manage energy efficiency in hybrid and electric vehicles (EVs). These boards must be designed to handle high voltages, manage heat dissipation, and protect sensitive components.
- Key Requirements: High voltage tolerance, heat management, energy efficiency
- Applications: Power conversion, electrical distribution, battery management systems (BMS)
6. Climate Control Systems
Climate control systems, including heating, ventilation, and air conditioning (HVAC) systems, use PCBs to manage sensors, control units, and actuators that regulate the interior temperature and air quality. The PCBs in these systems are responsible for controlling air temperature, humidity, airflow direction, and fan speed based on sensor feedback and user inputs.
- Key Requirements: Environmental resistance, real-time feedback control, reliability
- Applications: HVAC control units, temperature sensors, airflow control systems
7. Digital Displays and Instrumentation
Digital displays in modern vehicles, such as dashboards, instrument clusters, and heads-up displays (HUDs), rely on PCBs to process and display real-time information to drivers. These boards must integrate with various sensors and controllers, ensuring accurate readings of vehicle speed, fuel levels, engine performance, and other critical data.
- Key Requirements: High-resolution display support, low power consumption, signal processing
- Applications: Instrument clusters, heads-up displays, infotainment screens
8. Advanced Driver Assistance Systems (ADAS)
Advanced Driver Assistance Systems (ADAS) use a variety of sensors and cameras to provide safety features such as collision avoidance, lane departure warnings, and adaptive cruise control. PCBs in ADAS systems process sensor data, control algorithms, and communication with other vehicle subsystems to ensure safety-critical functions operate with high precision and low latency.
- Key Requirements: Real-time processing, sensor integration, high reliability
- Applications: Radar and lidar sensors, camera modules, collision avoidance systems
9. Transmission Sensors and Control Systems
Transmission sensors monitor the performance and health of the vehicle's transmission, helping to maintain smooth gear shifts and prevent mechanical failure. PCBs in transmission systems must be capable of handling high-frequency signals and integrating with other vehicle systems to provide feedback on engine load, speed, and shift timing.
- Key Requirements: High-frequency performance, signal processing, real-time feedback
- Applications: Transmission control units, shift sensors
10. Theft Prevention and Security Systems
Theft prevention systems, including vehicle immobilizers, alarms, and remote keyless entry systems, use PCBs to manage sensor inputs and transmit security data. These systems must operate under challenging environmental conditions and be capable of securely encrypting communication between the vehicle and its key fob or smartphone.
- Key Requirements: Signal security, encryption, low power consumption
- Applications: Vehicle security, keyless entry systems, immobilizers
11. Windshield Wiper and Lighting Control
PCBs in windshield wiper systems and lighting controls manage the actuation of wipers, headlights, and other exterior lighting systems. These systems must be designed to handle wet conditions, vibrations, and temperature extremes while ensuring proper operation of lighting and visibility features.
- Key Requirements: Wet environment resistance, vibration resistance, long lifespan
- Applications: Wiper control, headlight and fog light management, signaling systems
Why Choose Custompcba for Your Automotive PCB Needs?
- Expertise in Automotive Applications: Tailored PCB solutions for critical systems such as safety, power management, and communication.
- High Standards of Reliability: PCBs designed for long-lasting performance in harsh automotive environments.
- Advanced Prototyping and Testing: Rapid prototyping, rigorous testing, and DFM (Design for Manufacturability) support to ensure optimal designs.
- Compliance with Industry Standards: Adherence to ISO 9001:2015, IATF 16949, and PPAP for quality assurance.
If you’re looking to develop your next automotive PCB solution, Custompcba is your trusted partner for delivering reliable, high-performance products. Let us help you drive innovation in the automotive industry with advanced PCB technology.