While FR4 is the go-to material for many printed circuit board (PCB) applications due to its affordability and reliability, it is not the only option available. Depending on the specific needs of your application, alternative PCB materials may offer advantages that better suit your requirements.
One such material is polyimide, which offers unique properties that can be highly beneficial for certain industries and applications. Understanding the characteristics of polyimide PCBs is crucial for selecting the right material for your projects, especially if you are new to the PCB manufacturing process.
In this article, we will explore the key properties of polyimide PCBs and discuss scenarios where they may provide superior performance compared to traditional FR4 boards. By understanding these factors, you will be better equipped to determine if polyimide is the ideal choice for your specific application needs.
Overview of Polyimide PCB Materials
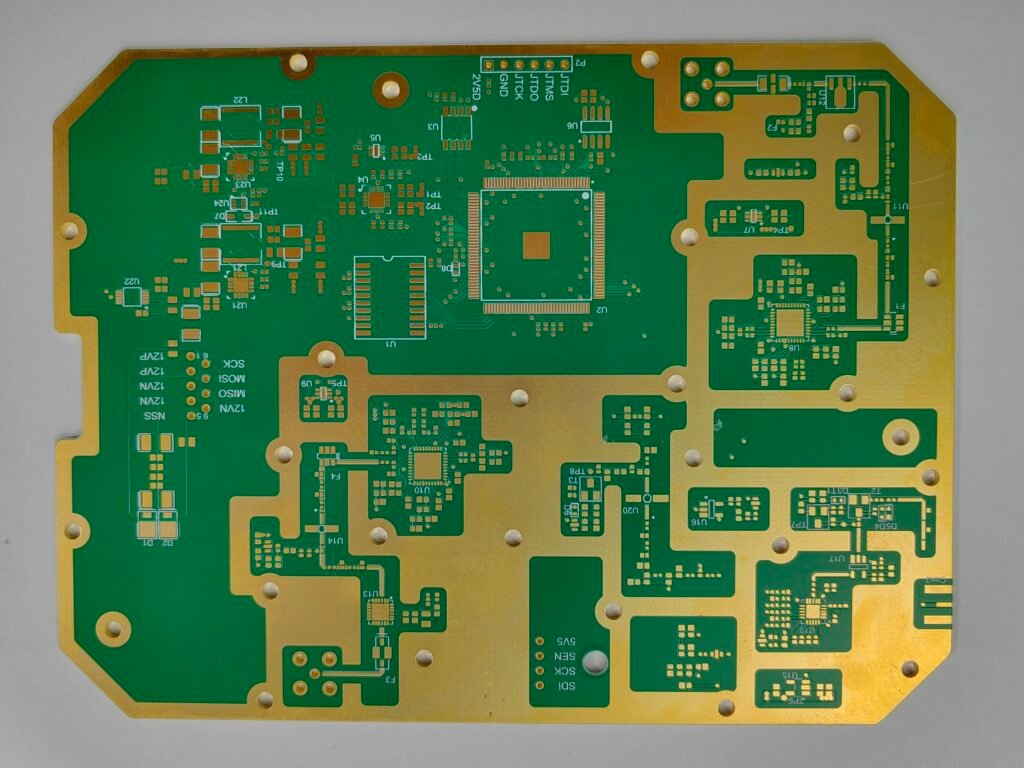
Polyimide (PI) is a high-performance synthetic polymer made from imide monomers, widely used in electronics manufacturing, particularly in high-performance printed circuit board (PCB) materials. Polyimide is the material of choice in industries such as aerospace, defense, automotive, and consumer electronics, owing to its excellent thermal stability, chemical resistance, flexibility, and electrical properties.
Polyimide is a polymer, typically synthesized from organic compounds containing imide structures. Depending on the production process and additives used, polyimide can be divided into different types, each with its own set of advantages, catering to the diverse needs of various industries and applications.
Types of Polyimide PCBs
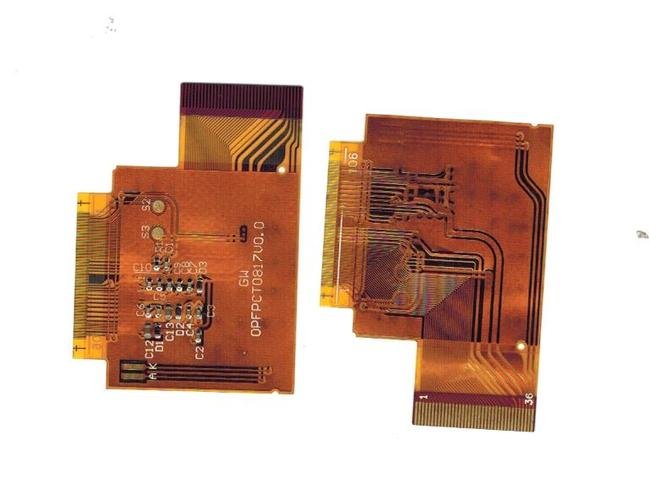
Pure Polyimide (Second-Generation Polyimide)
Pure polyimide typically does not include any flame retardants or other chemical additives. It offers exceptional thermal stability and heat resistance, making it suitable for extreme operating conditions. Pure polyimide is commonly used in high-end applications requiring high heat resistance and stability.
Third-Generation Polyimide
Third-generation polyimide materials incorporate specific flame retardant additives, significantly enhancing the material's flame resistance. While their thermal stability is slightly lower than that of second-generation polyimide, they offer shorter curing times and lower curing temperatures, making them more efficient in production. These materials are suitable for applications requiring lower-temperature curing processes.
Filled Polyimide
Filled polyimide is a composite material where polyimide is combined with fillers such as inorganic substances. These fillers help reduce shrinkage during the curing process, minimizing the formation of cracks. This material is primarily used in environments requiring higher mechanical strength and crack resistance, especially when high pressure is involved during production.
Low-Flow Polyimide
Low-flow polyimide is created by adding flow restrictors, reducing the material’s flexibility to meet specific application requirements. The main feature of this material is its ability to provide high-strength electrical insulation while maintaining low flowability, which is especially important for certain precision electronic products.
Key Properties of Polyimide PCBs
Polyimide, as a PCB substrate, exhibits several unique advantages, making it ideal for high-performance and high-reliability applications:
Outstanding Thermal Stability
Polyimide boasts extremely high thermal stability, allowing it to operate in environments up to 260°C without degradation of its structure or electrical performance. This makes polyimide the ideal choice for high-temperature applications, such as aerospace, automotive electronics, and industrial control.
Exceptional Flexibility
Polyimide PCBs are typically used to manufacture flexible circuits, offering excellent flexibility and stretchability. Whether for high-frequency signal transmission, electrical connections, or complex circuit designs in three-dimensional spaces, polyimide provides outstanding support. It easily meets the growing demand for flexible circuits in modern electronic products.
Excellent Tensile and Mechanical Strength
Polyimide not only offers high flexibility but also possesses strong tensile and compressive strength. This enables it to withstand substantial physical stress without damage. These characteristics make polyimide particularly suitable for electronic products with high physical requirements.
Superior Chemical Resistance
Polyimide demonstrates excellent resistance to chemicals such as solvents, oils, acids, and alkalis, making it ideal for environments where exposure to chemicals is common. For example, automotive electronics and industrial control devices that may be exposed to chemicals for prolonged periods benefit from polyimide’s ability to maintain its structural integrity.
Low Dielectric Constant and Low Loss
Polyimide has a low dielectric constant and low electrical loss characteristics. This allows for excellent electrical performance in high-speed, high-frequency applications, supporting signal transmission while reducing signal attenuation and reflection, ultimately improving overall circuit performance.
Exceptional Environmental Aging Resistance
Polyimide is highly resistant to ultraviolet (UV) light, oxidation, and aging. Even in extreme environmental conditions, the material's mechanical and electrical properties remain stable, extending the lifespan of electronic products.
Superior Electrical Properties
In addition to its excellent insulating properties, polyimide maintains stable electrical performance in both low and high-temperature environments. It has high dielectric strength, effectively isolating different electrical layers and preventing short circuits and current leakage.
Applications of Polyimide PCBs
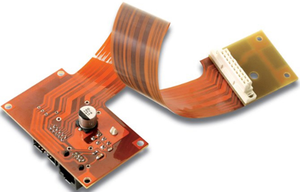
Due to its superior characteristics, polyimide PCB is widely used across various high-tech industries:
- Aerospace: Polyimide ensures the long-term stable operation of electronic devices in high-temperature and high-vibration environments, making it ideal for use in spacecraft, satellites, and unmanned aerial vehicles.
- Military Electronics: The chemical stability and high-temperature resistance of polyimide make it a crucial material for high-end electronic devices used in military applications.
- Automotive Electronics: Polyimide flexible PCBs are well-suited for complex automotive environments, including sensors, navigation systems, and control units that must operate in high-temperature conditions.
- Medical Equipment: In medical devices requiring high reliability and resistance to environmental aging, polyimide is used for manufacturing small, high-density circuit boards to ensure long-term stable performance.
- Consumer Electronics: Polyimide is used in flexible circuit boards (FPC) or rigid-flex PCBs for high-tech consumer electronics like smartphones and wearable devices.
- Industrial Control: Due to its high thermal stability and chemical resistance, polyimide is an essential PCB material for industrial automation and control systems, ensuring reliable operation in extreme conditions.
Polyimide PCBs vs. FR4 Materials
FR4 is the most commonly used PCB substrate material and is suitable for most standard electronic applications. However, compared to polyimide, FR4 has limitations, particularly in high-temperature and chemical environments. As a high-performance material, polyimide outperforms FR4 in extreme operating conditions, such as high-frequency, high-temperature, and high-pressure environments. Polyimide offers higher thermal stability, greater flexibility, and better chemical resistance, making it the material of choice in applications with stringent performance requirements.
Polyimide PCB Materials and Their Applications
Polyimide (PI) is a high-performance polymer known for its excellent thermal stability, chemical resistance, mechanical strength, and electrical properties. These characteristics make polyimide widely used in the electronics industry, particularly in the manufacturing of high-end printed circuit boards (PCBs). Polyimide materials are especially favored in the production of flexible and rigid-flex PCBs, which have gained significant popularity in recent years and are expected to continue growing in market share from 2017 to 2027.
Applications of Polyimide PCB Materials
Polyimide PCB materials are widely used in several high-demand industries due to their exceptional performance characteristics:
- Computer Electronics
In computer systems and laptops, especially mobile devices, PCBs need to be flexible, heat-resistant, and vibration-resistant. Polyimide flexible PCBs are well-suited for these environments because of their superior thermal stability, mechanical strength, and ability to withstand physical stress during use. - Automotive Electronics
Modern vehicles increasingly rely on electronic systems, often using flexible PCBs to handle vibrations and thermal cycling in the automotive environment. Polyimide PCBs are ideal for automotive applications where robustness and reliability in harsh conditions are crucial. - Consumer Electronics
Consumer electronic products like smartphones and tablets, which are subject to frequent handling and wear, often utilize flexible or rigid-flex PCBs made from polyimide. These materials are essential for meeting the demands of miniaturization and high-performance electronic devices. - Medical Electronics
In medical applications, especially implantable devices, prosthetics, and imaging technologies, polyimide PCBs are preferred for their flexibility and durability. These properties are critical in devices that must conform to specific shapes and withstand motion and wear over time. - Aerospace and Military Electronics
Polyimide is commonly used in aerospace and military electronics due to its excellent thermal stability, mechanical strength, and chemical resistance. These sectors often require PCBs to perform reliably under extreme conditions and in demanding environments where frequent maintenance and repair are necessary.
Comparison Between Polyimide and FR4 PCB Materials
Overview of FR4 Material
FR4 is one of the most commonly used PCB materials and is typically made from glass fiber and epoxy resin. FR4 is the industry standard for most general applications because of its relatively low cost and good electrical insulating properties. However, FR4 has limitations in high-temperature and high-frequency environments, where its performance may degrade.
Comparison of Polyimide and FR4
- Thermal Stability
Polyimide outperforms FR4 in thermal stability, with the ability to withstand operating temperatures up to 260°C, compared to FR4’s typical range of 130°C to 150°C. This makes polyimide the preferred choice for high-temperature applications such as automotive, aerospace, and industrial electronics. - Mechanical Strength and Flexibility
Polyimide PCBs offer superior flexibility and tensile strength, making them ideal for applications that require bending, complex designs, or high-vibration environments. In contrast, FR4’s rigidity may pose limitations in these situations, especially in devices where flexibility and miniaturization are key. - Chemical Resistance
Polyimide offers excellent resistance to a broad range of chemicals, including fuels, oils, and solvents, which are commonly encountered in automotive, aerospace, and military applications. While FR4 also provides some chemical resistance, polyimide’s superior long-term resistance to corrosion makes it more suitable for extreme environments. - Electrical Performance
Polyimide has a lower dielectric constant and lower electrical losses compared to FR4, making it more suitable for high-frequency applications. FR4, while adequate for low-frequency circuits, tends to perform poorly in high-frequency or high-speed applications, where signal integrity is critical.
When to Choose Polyimide PCB Materials Over FR4
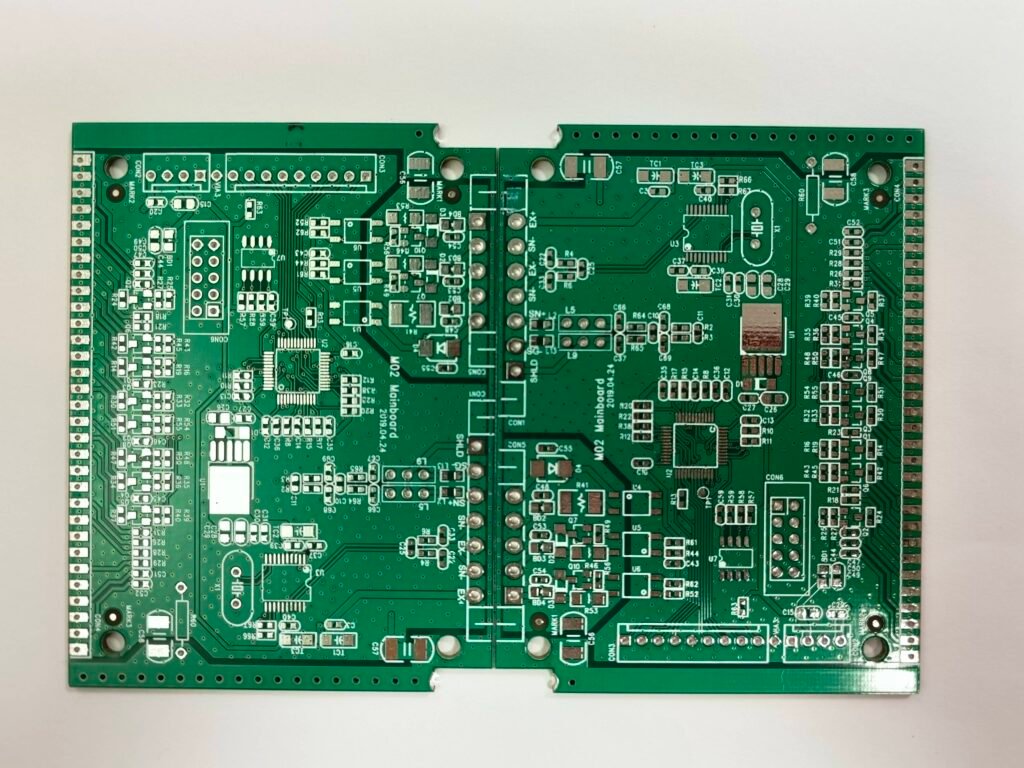
While FR4 is the material of choice for most general-purpose applications due to its low cost and availability, polyimide is a better fit for certain high-performance and specialized applications. Here are scenarios where polyimide is the preferred choice:
- High-Temperature Environments
For applications that operate in high-temperature conditions, such as automotive electronics, aerospace, and industrial control systems, polyimide’s superior heat resistance makes it the ideal choice. - High-Frequency Applications
Polyimide’s low dielectric constant and low electrical loss properties make it ideal for high-frequency circuit applications, such as in RF communications, where maintaining signal integrity is essential. - Flexible Applications
Polyimide is highly flexible, making it suitable for flexible and rigid-flex PCBs used in compact and complex device designs where traditional rigid PCBs like FR4 are impractical. - Long-Term Durability
Polyimide’s durability makes it an excellent choice for electronics that need to perform reliably over long periods, such as medical devices, military equipment, and aerospace applications.
Although polyimide is generally more expensive than FR4, its superior performance characteristics make it cost-effective in the long term, especially in applications that demand flexibility, reliability, and thermal performance.
Conclusion
Polyimide PCB materials have proven to be a vital component in the development of advanced electronic systems across various industries. Their outstanding thermal stability, chemical resistance, flexibility, and electrical properties make them the material of choice for applications requiring high performance in harsh environments. While FR4 remains the go-to material for general-purpose PCBs, polyimide offers a significant advantage in applications where durability, flexibility, and reliability are critical. As the demand for high-performance, miniaturized, and flexible electronics continues to grow, the role of polyimide in PCB manufacturing is set to expand.