Soldering plays a crucial role in the design and assembly of printed circuit boards (PCBs). It’s the only reliable method to securely attach components to the board and ensure their long-term stability. Without soldering, there would be no PCB. However, not all soldering techniques are the same, and it’s important to distinguish between two key methods: wave soldering and reflow soldering.
In PCB assembly, the two primary soldering methods are wave soldering and reflow soldering. What sets these techniques apart, and how can you determine which one to use for your specific needs? Let’s dive into the differences and help clarify when each method is most appropriate.
What is Wave Soldering?
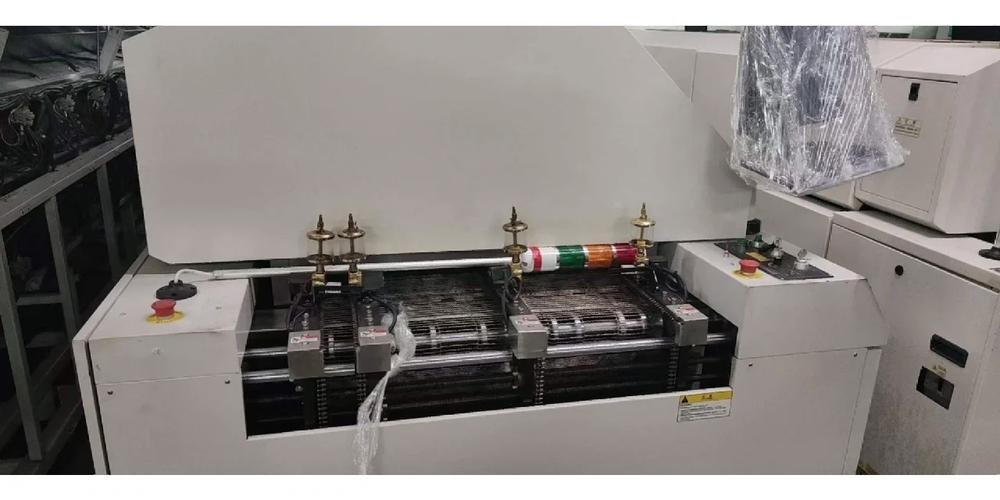
Wave soldering is a mass-production technique used to efficiently solder multiple PCBs (Printed Circuit Boards) in a short amount of time. The process involves passing each PCB over a bath of molten solder. A pump generates a "wave" of solder that flows across the surface of the board, creating the necessary connections between the components and the PCB pads. After the soldering process, the board is cooled either through water spraying or air blowing to solidify the solder joints and secure the components in place.
Wave soldering offers a highly efficient solution for bulk manufacturing, particularly for through-hole components. However, precise control over the process is essential. Temperature regulation plays a crucial role in avoiding potential issues such as mechanical stress that could lead to cracks or loss of conductivity. Inadequate preheating can cause voids in the solder joints, compromising both the structural integrity and electrical performance of the board. Incorrect soldering temperatures can also lead to an improper solder thickness, making the PCB more susceptible to stress during operation.
What is Reflow Soldering?
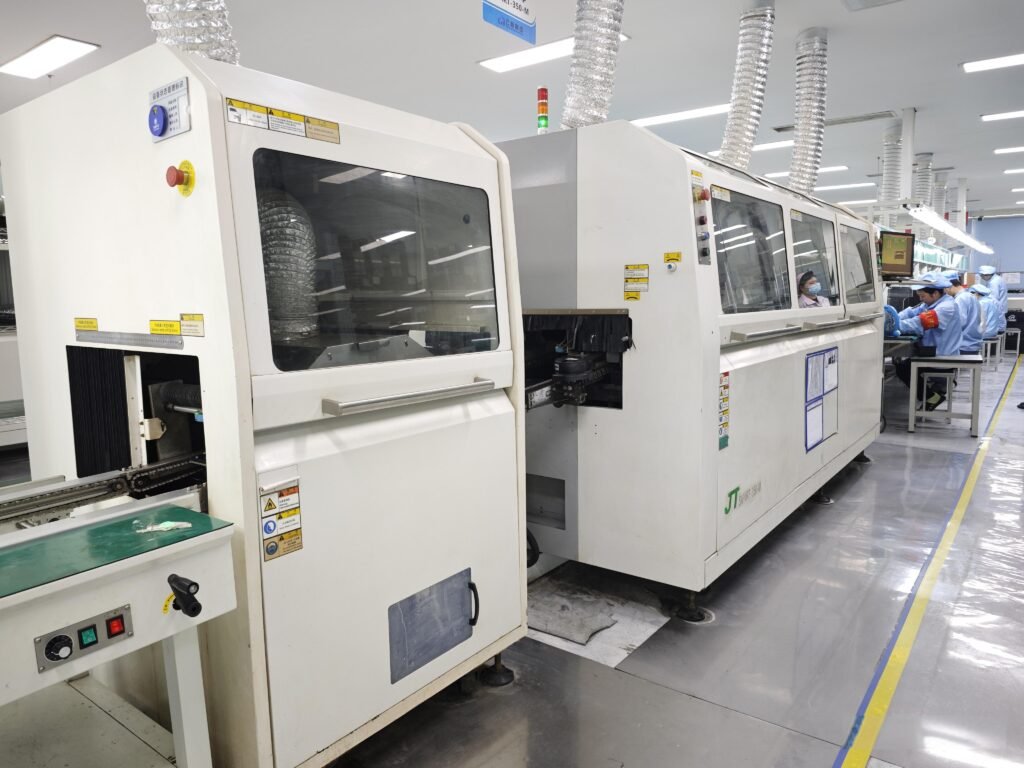
Reflow soldering is a widely used method for attaching surface-mount devices (SMDs) to PCBs. Unlike wave soldering, which is generally used for through-hole components, reflow soldering is particularly suited for attaching SMDs. In this process, solder paste—which consists of flux and powdered solder—is applied to the PCB pads where components will be placed. Once the components are positioned on the solder paste, the entire assembly is heated in a reflow oven or with infrared lamps. The heat causes the solder paste to melt, creating strong electrical and mechanical connections between the components and the PCB pads. If needed, individual joints can be soldered using a hot air pencil.
Reflow soldering is a more controlled process compared to wave soldering, with fewer environmental variables to monitor. The heating process in reflow soldering can be carefully calibrated, minimizing the risks of thermal damage to components. It’s ideal for manufacturing surface-mount components and is often used in smaller production runs, especially when higher precision is required.
Wave Soldering vs. Reflow Soldering: Key Differences
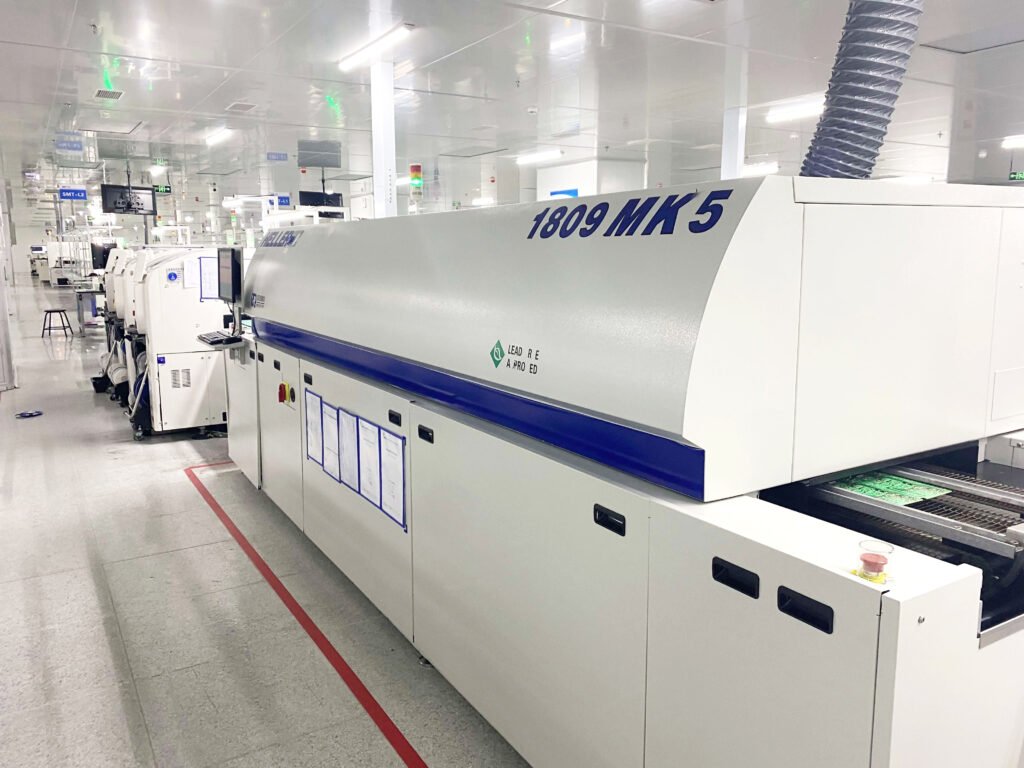
So, when should you choose one soldering technique over the other? The decision largely depends on the type of components being used, the design of the PCB, production volume, and cost considerations.
1. Component Type:
- Wave Soldering: Primarily used for through-hole components, where the leads pass through the board and need to be soldered on both sides. It’s less common for surface-mount devices, though it can be adapted for them.
- Reflow Soldering: Ideal for surface-mount components (SMDs), where components are placed on the surface of the PCB without leads passing through.
2. Production Volume:
- Wave Soldering: Often used for high-volume manufacturing, where speed and cost-efficiency are critical. It’s ideal for large batches of PCBs where through-hole components are involved.
- Reflow Soldering: While it can be used for large production runs, it’s more commonly employed for smaller volumes or complex designs where precision is key. Reflow soldering is often the choice for low- to medium-volume productions.
3. Complexity and Control:
- Wave Soldering: More complex to control due to the need for precise temperature regulation and management of the board's interaction with the solder wave. Failure to create the right conditions can lead to defects such as cold joints, solder bridges, or excessive stress on the board.
- Reflow Soldering: Offers more consistent results as it involves precise control of the heating process. The ability to profile temperature cycles ensures that components are heated in a controlled manner, reducing the risk of damage.
4. Cost and Speed:
- Wave Soldering: Generally faster and more cost-effective, especially for high-volume manufacturing of through-hole PCBs. The process is less labor-intensive and doesn’t require as much manual oversight.
- Reflow Soldering: While slower than wave soldering, it is still cost-effective for certain applications, especially those involving intricate SMDs or high-density components. However, the equipment required for reflow soldering can be more expensive, especially for small production runs.
5. Flexibility:
- Wave Soldering: Less flexible compared to reflow soldering. The setup and process are typically optimized for through-hole components, and making adjustments for other types of components can be challenging.
- Reflow Soldering: More adaptable to varying types of PCB designs, including complex mixed technology boards that contain both SMDs and through-hole components.
Using Both Methods: Hybrid Soldering
In some cases, manufacturers may use a combination of both wave soldering and reflow soldering, depending on the specific needs of the PCB assembly. For example, surface-mount components can be attached using reflow soldering on one side of the board, while through-hole components are wave soldered on the other. This hybrid approach can provide the benefits of both methods while optimizing the overall production process.
Conclusion
Choosing between wave soldering and reflow soldering depends on several factors, including the type of components, the volume of production, and the required precision. Wave soldering is generally preferred for high-volume, through-hole component production, while reflow soldering is more suited to smaller, surface-mount component assemblies. Understanding the strengths and limitations of each method will help you select the most appropriate technique for your PCB assembly needs.