An In-Depth Analysis of Surface Mount Technology (SMT)
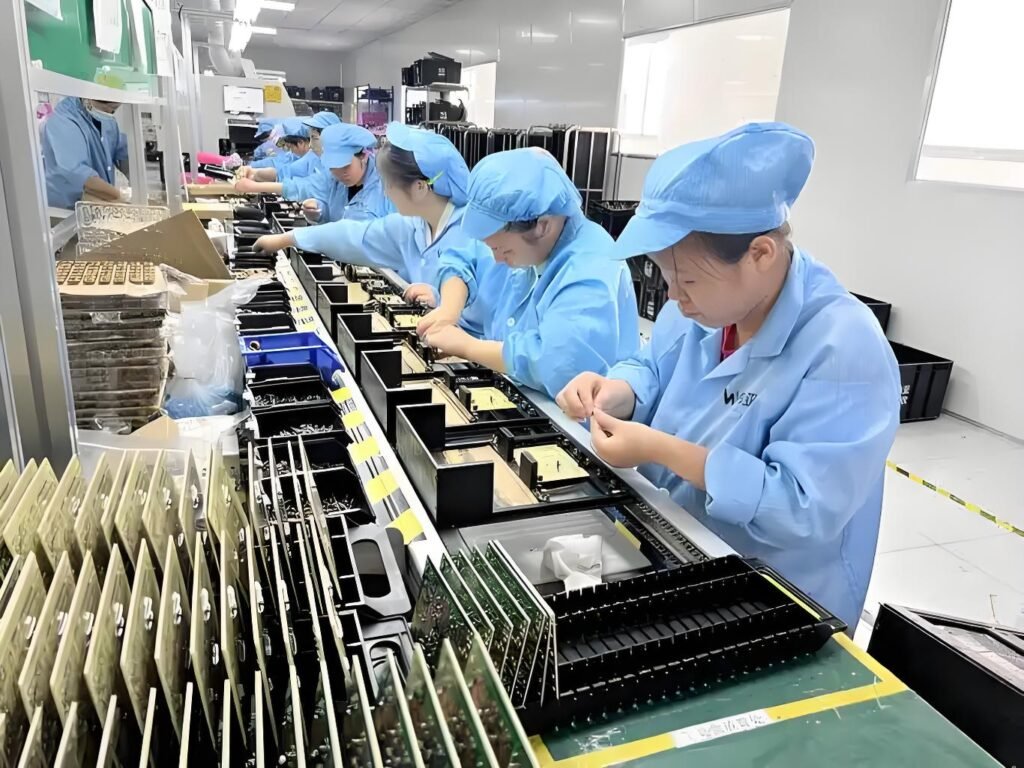
Surface Mount Technology (SMT) is a modern electronic assembly process that involves placing components directly onto the surface of printed circuit boards (PCBs), rather than relying on traditional through-hole connections. This technology plays a crucial role in the production of electronic products, making the assembly process more efficient and precise.
Since its widespread adoption in the 1980s, SMT has quickly become the standard in the electronics manufacturing industry. This shift is primarily due to its high degree of automation, which significantly reduces both manufacturing and assembly time and costs. Traditional methods required manual connections of components through holes in the circuit board, increasing labor costs and the risk of human error. In contrast, SMT automates the placement of components, minimizing human factors and improving overall production efficiency.
Another notable advantage of SMT is its ability to support higher component density and smaller sizes. This allows designers to incorporate more functionality within limited spaces, enhancing product performance. Additionally, SMT enables components to be mounted on both sides of the circuit board, further optimizing space utilization and design flexibility.
Furthermore, Surface Mount Technology exhibits excellent pressure performance, making it suitable for various application needs. These advantages have made SMT the preferred assembly method for many high-tech electronic products, driving continuous innovation and development in the industry. By utilizing SMT, manufacturers can meet the growing market demands while improving product quality and reliability.
Overview of the Typical SMT Process
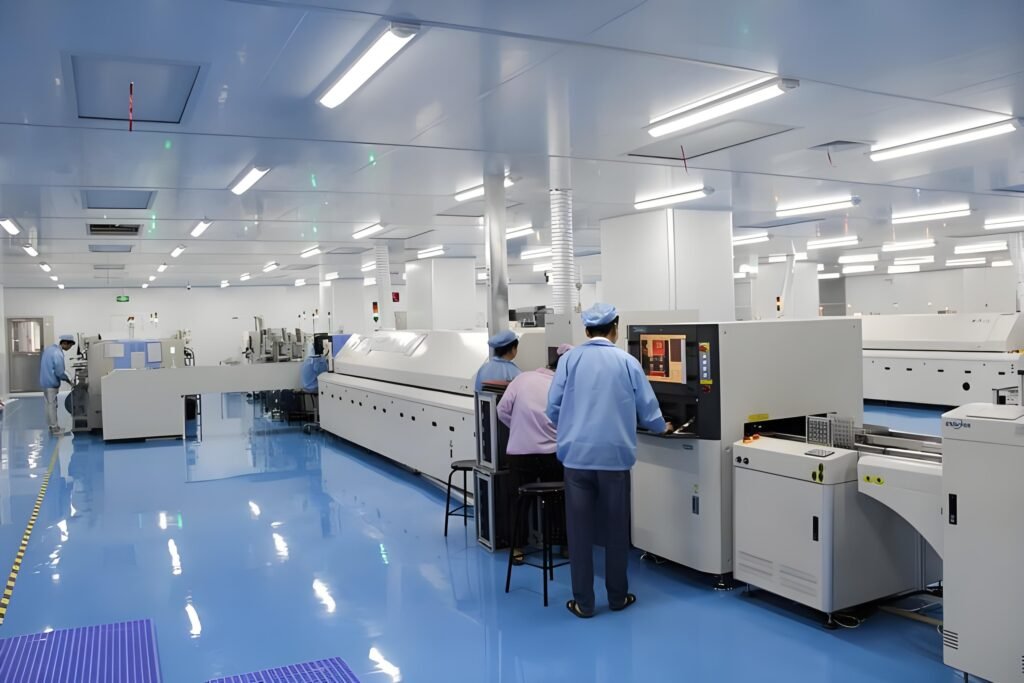
The Surface Mount Technology (SMT) process consists of three key steps: solder paste printing, component placement, and reflow soldering. These steps work in tandem to ensure high quality and efficiency in the final product.
Solder Paste Printing
Solder paste printing is the initial phase of the SMT process, involving the even application of solder paste onto the pads of a printed circuit board (PCB). This process is typically carried out using automated printing machines to ensure accuracy and speed.
During this stage, the printer uses a pre-made PCB stencil and a squeegee to apply solder paste to each pad. The solder paste, a mixture of flux and solder, is essential for connecting surface mount components (SMCs) to the PCB pads. To ensure effective solder joints, the correct amount of solder paste must be applied to each pad. If the paste is unevenly applied, it will not form effective connections during the reflow soldering process.
Quality control in solder paste printing is critical, as any printing defects that go undetected at this stage can lead to more severe issues in subsequent steps. Template design should be optimized, and the assembly team must exercise caution to ensure the process is repeatable and stable. Many solder paste printers are equipped with automatic inspection features to verify the thickness and uniformity of the paste.
In some cases, external inspection equipment, such as solder paste inspection machines using 3D technology, may also be employed for more in-depth checks. These devices can measure the volume of solder paste, not just the printed area, providing a more comprehensive quality assessment.
Component Placement
Once the PCB passes inspection, it enters the component placement stage of the SMT assembly process. In this phase, automated equipment uses vacuum nozzles or grippers to pick up each component from packaging and place it accurately onto the designated positions on the PCB.
Modern SMT equipment not only boasts high placement accuracy but also operates at remarkable speeds. Some advanced machines can place up to 80,000 individual components per hour. This efficient component placement significantly boosts production efficiency and reduces manufacturing lead times.
After all components are placed on the PCB, they must undergo inspection to ensure correct placement. This step is crucial because failing to identify any placement errors before soldering can lead to costly rework and time delays.
Reflow Soldering
After component placement and inspection, the process moves into the reflow soldering phase. In this part of the SMT process, the PCB is placed into a reflow soldering machine (commonly referred to as a reflow oven).
During this stage, all electrical solder connections are formed between the components and the PCB. Heat is applied to transform the previously applied solder paste into solder, creating secure connections.
Accuracy during reflow soldering is essential. If the PCB is heated too much, components may be damaged; conversely, if the temperature is too low, effective connections may not form. To ensure optimal results, all PCBs are placed on a conveyor belt inside the soldering machine, where they gradually pass through a series of heating zones before moving into a cooling zone.
In each heating zone, the PCB must remain for the appropriate duration to prevent solder joint defects. Additionally, the PCB must completely cool before handling or moving to avoid warping or other physical damage.
After passing through the reflow soldering machine, the PCBs undergo a final inspection, typically performed by a 3D Automated Optical Inspection (AOI) system. This inspection ensures that the solder joint quality meets expectations and that no errors occurred during the SMT process. Machines used for this step are faster and more accurate than human inspectors, contributing to overall production quality.
Through these steps, the SMT process achieves efficient and precise assembly of electronic products. In the electronic manufacturing sector, as technology continues to advance and market demands grow, SMT will play a vital role in driving industry development.
The Importance of SMT and Its Future Development Directions
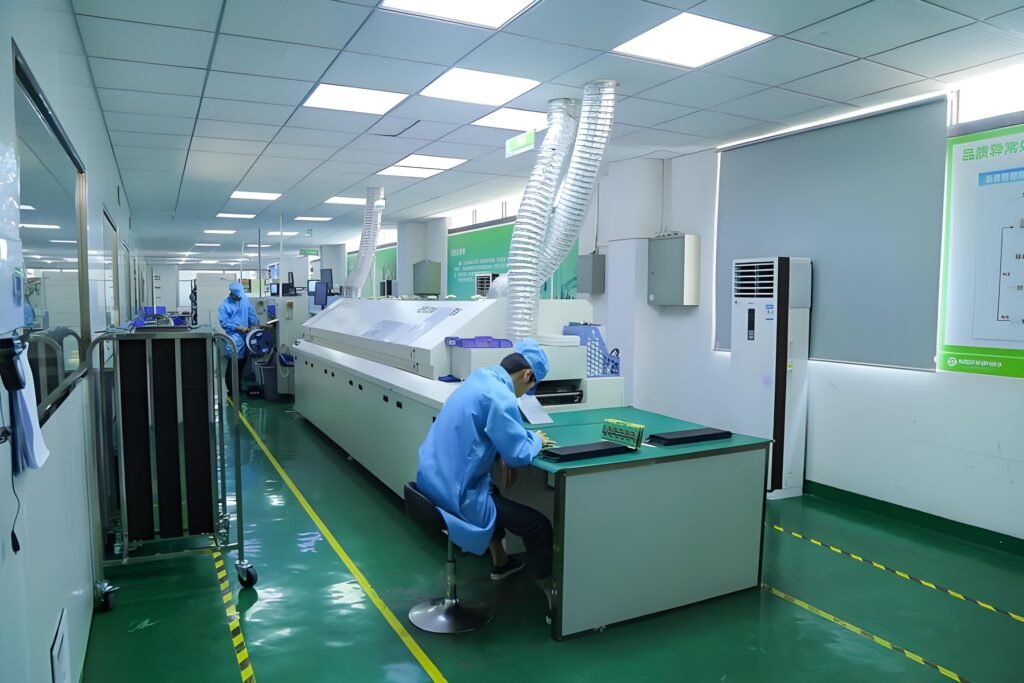
Surface Mount Technology (SMT) plays an irreplaceable role in the manufacturing of electronic products. Compared to traditional through-hole technology, SMT offers higher component density, smaller mounting space, and better electrical performance. This technology not only supports double-sided assembly but also allows for more complex circuit designs, meeting the increasing demands for functionality and performance in modern electronic products.
Additionally, the high degree of automation in SMT significantly enhances production efficiency, reduces human errors, and ensures stable product quality. As the industry continues to demand higher precision and reliability, SMT is advancing in material selection and process innovation to adapt to various emerging applications and technological challenges.
Therefore, SMT is not just a manufacturing technique; it is a key factor driving the development of the electronics manufacturing industry. By continuously optimizing SMT processes, companies can maintain a competitive edge in the market and promote product innovation and sustainable development.
Final Summary
In today’s rapidly evolving electronic manufacturing industry, Surface Mount Technology (SMT) provides companies with the drive for innovation and competitiveness. At CustomPCBA, we are committed to delivering high-quality custom PCBA solutions to meet a variety of needs. If you are interested in our services or have any questions, please feel free to contact us. We look forward to collaborating with you to drive the success of your projects.