PCB Drill Bits: The Importance of Key Equipment in Printed Circuit Board Manufacturing
In modern electronic products, printed circuit boards (PCBs) serve as the essential components that connect and support various electronic elements. Within the manufacturing process of PCBs, drilling technology plays a critical role, directly affecting the performance and reliability of the circuit boards. PCB drill bits, as indispensable machinery in this process, are responsible for accurately creating holes in the circuit boards to ensure the precision of every electrical connection point.
To achieve high-precision drilling, PCB drill bits utilize advanced technologies and materials, enabling efficient operation in multi-layer circuit boards while meeting stringent manufacturing standards. Accurate drilling is crucial, not only for the installation of subsequent components but also for the overall performance and stability of the circuitry. This article will delve into the working principles, design features, and real-world applications of PCB drill bits, showcasing how we at ABL Circuits leverage these high-precision tools to enhance manufacturing processes and product quality. Additionally, we will share best practices and innovative techniques related to the drilling process to help you better understand the critical role this essential step plays in electronic manufacturing.
Understanding PCB Drilling: A Key Process in Circuit Board Manufacturing
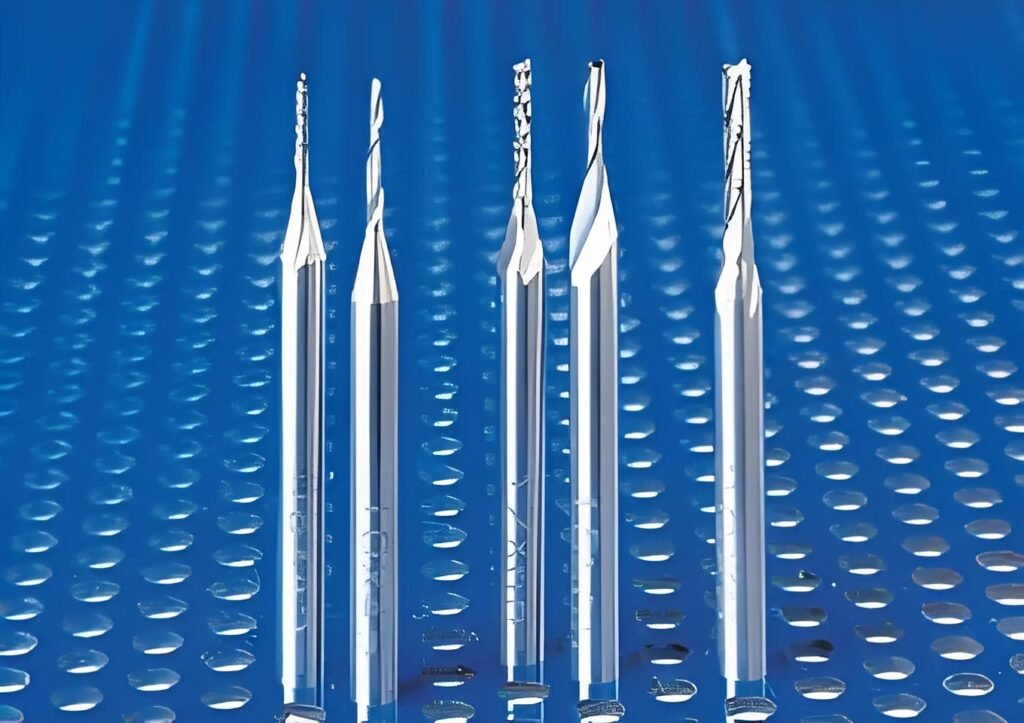
PCB drilling, often referred to as printed circuit board drilling, is a fundamental process that involves creating holes, slots, and various cavities on electronic circuit boards. This technique is essential for establishing electrical connections and mechanical support for components within the circuit.
During the PCB drilling process, several types of holes are created, including plated through holes (PTH), blind vias, buried vias, and microvias. Each of these types serves specific functions, facilitating electrical connectivity between different layers of the circuit board or allowing for component placement.
Given the high precision required in this operation, specialized equipment is utilized, such as manual or laser-guided PCB drill bits. These advanced tools ensure accuracy and consistency in hole size and placement, we employ drill bits equipped with laser detection technology, which guarantees concentricity and the correct drill diameter ranging from 0.1 mm to 6.5 mm, even in automated processes. This innovative approach enhances the reliability and quality of the final product, ensuring that each circuit board meets stringent industry standards.
In summary, PCB drilling is a crucial step in the manufacturing process that directly impacts the performance and functionality of electronic devices. By utilizing state-of-the-art drilling techniques and equipment, manufacturers can achieve the necessary precision to produce high-quality circuit boards.
The Importance of Drilling in the PCB Manufacturing Process
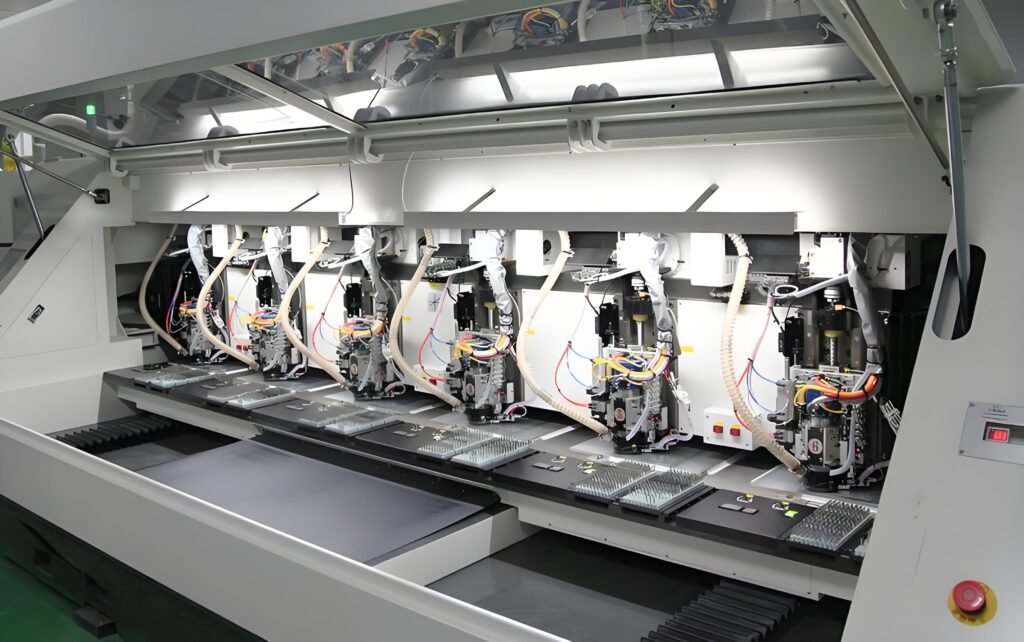
Drilling is a critical step in the manufacturing process of printed circuit boards (PCBs), often regarded as one of the most expensive and time-consuming parts of the entire process. This is due to the need for extreme precision in this step to ensure that the final product meets the highest quality standards. Any deviation in drilling can lead to poor electrical connections, ultimately affecting the performance and reliability of the entire circuit board.
The manufacturing process of PCBs is complex and typically includes about 20 key steps. Generally, the drilling phase occupies a starting position in the overall production process, following the cutting of the substrate materials and the determination of the required thickness of the PCB. Once the substrate is prepared, the drilling process commences, marking the official beginning of manufacturing.
During the preparation for drilling, a tool pin is first inserted to secure the circuit board in a pre-programmed computer numerical control (CNC) machine. This type of equipment can drill component mounting holes and vias with extreme precision on the PCB. Next, the circuit board is segmented, and its accuracy is meticulously measured to ensure compliance with design specifications and electrical performance standards.
After drilling is completed, a conveyor belt polishing machine cleans the copper surface to remove any tiny burrs or rough edges. This step not only enhances the aesthetic quality of the product but also prevents issues that could arise during subsequent processing and soldering. A clean surface helps improve soldering effectiveness, thereby strengthening the connections between components and the PCB.
Once the PCB passes rigorous quality control checks, the drilling phase concludes, and the subsequent manufacturing steps begin, such as metallization, gold plating, and printing. The success or failure of this phase directly impacts the smooth progress of later production steps, emphasizing its significance within the entire PCB manufacturing process. An accurate drilling process lays a solid foundation for the entire production line, ensuring that the final product meets customer requirements and high market standards.
What Machines Do We Use at CustomPCBA? How Accurate Are They?
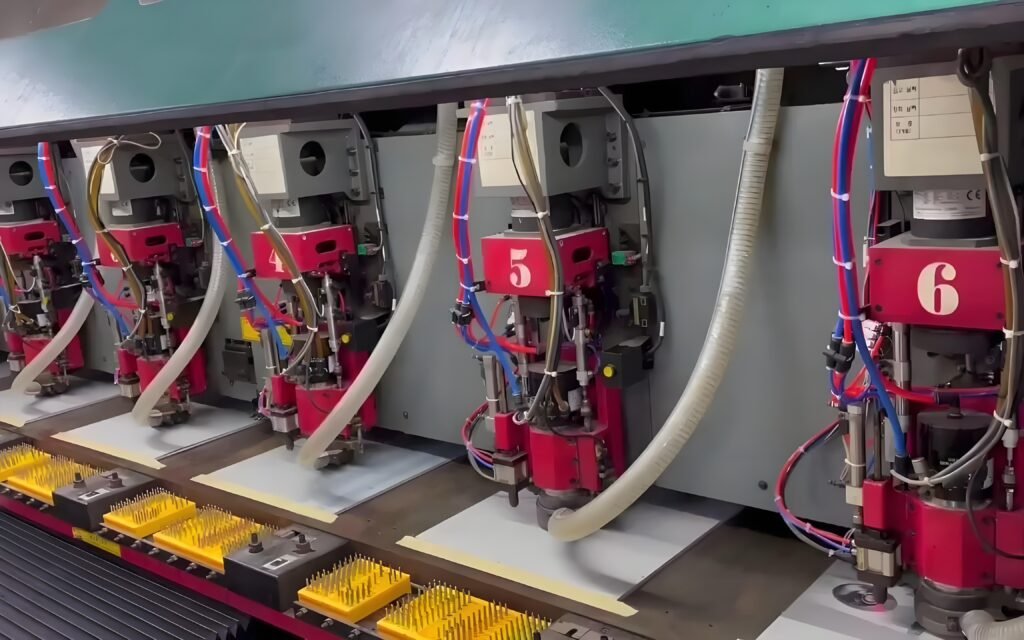
At CustomPCBA, we utilize the advanced DRB 610 1+1 series PCB drilling machine to meet our high-precision manufacturing needs. Precision is crucial in the PCB drilling process, as even the slightest deviation can impact the quality and performance of the final product. Notably, the DRB 610 1+1 series boasts an accuracy of up to 0.0005 millimeters.
To put this precision into perspective, the average diameter of human hair is approximately 0.0254 millimeters, meaning the accuracy of the DRB 610 is about 50 times that of a human hair. This exceptional precision allows us to achieve high-quality electrical connections during the manufacturing process, ensuring the reliability and performance of the PCBs.
In addition to its precision, the design of the DRB 610 1+1 series also emphasizes high efficiency. This equipment is capable of quickly handling large production volumes while maintaining consistent quality standards. Our DRB 610 drilling machine is equipped with an advanced laser detection system that monitors the alignment of the drill holes in real-time, ensuring that each hole meets design specifications, even in unmanned operation scenarios, thus guaranteeing high concentricity and accuracy.
By employing the DRB 610 1+1 series PCB drilling machine, CustomPCBA not only enhances production efficiency but also strengthens quality control throughout various stages of PCB manufacturing. The use of this equipment enables us to provide our customers with more reliable and high-quality products, meeting the ever-growing market demands.
How Does It Work?
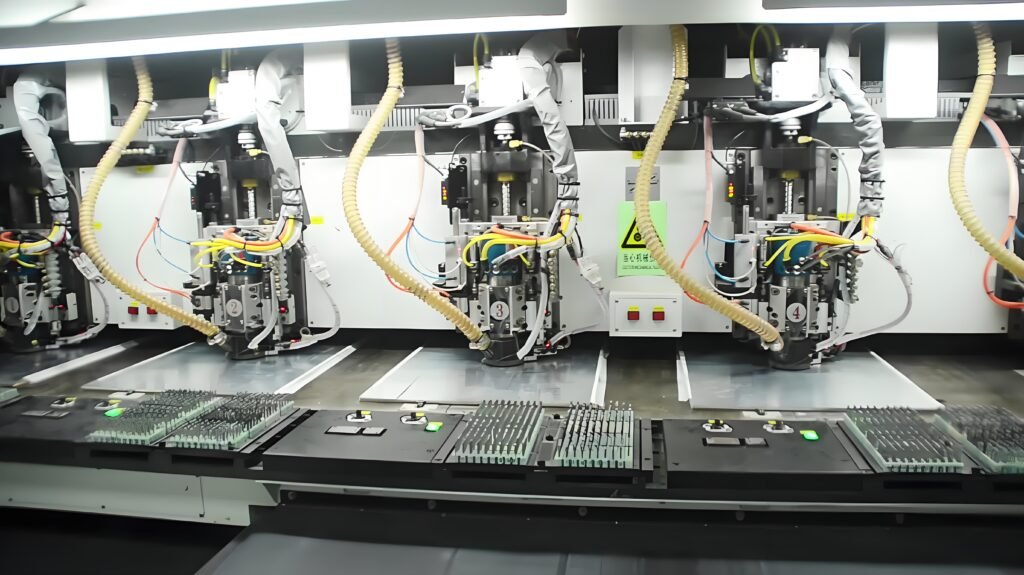
The DRB 610 1+1 series PCB drilling machine is part of Lenz’s redesigned and upgraded product line, which delivers exceptional precision and speed. This advanced machinery utilizes a combination of cutting-edge technologies to ensure accurate and efficient drilling processes.
One of the key features that enhance its precision is the use of foot pedal technology, which allows for fine control during operation. Coupled with a retractable loading system, this feature ensures that the PCB is securely held in place throughout the drilling process. Additionally, the integrated CCD (Charge-Coupled Device) camera system provides real-time feedback on alignment, further guaranteeing the accuracy of each drilled hole.
The DRB 610 1+1 series also incorporates advanced depth control for drilling and routing, which allows operators to set precise drilling depths for different applications. This capability, combined with a laser tool measurement system, ensures that every aspect of the drilling process is monitored and adjusted as needed. The use of Sieb & Meyer’s sophisticated controllers allows for seamless integration and enhanced operational efficiency.
One of the standout advantages of this machine is its ability to conduct trial runs before full-scale production. This functionality enables our team at CustomPCBA to identify and eliminate potential errors early in the manufacturing process, significantly reducing the risk of defects in the final product.
Moreover, the machine’s “pattern selection” feature allows for easy replication of drilling patterns. This not only streamlines the setup process but also minimizes production costs by reducing the time and resources needed for adjustments between batches.
In summary, the DRB 610 1+1 series PCB drilling machine exemplifies modern engineering excellence, offering high-speed, high-precision capabilities while ensuring reliability and cost-effectiveness in PCB manufacturing. This advanced technology allows CustomPCBA to consistently deliver top-notch products to our clients, meeting the demands of an ever-evolving market.
CustomPCBA: Leading the Way in Advanced PCB Manufacturing
For over 30 years, CustomPCBA has been at the forefront of cutting-edge PCB manufacturing services. We continually refine our processes to ensure we deliver the highest quality PCB products in the shortest time possible, meeting the evolving needs of our clients.
With our extensive expertise in the field, we offer a comprehensive range of PCB services tailored to meet your custom design, manufacturing, and assembly requirements. Whether you need a simple prototype or a complex multilayer board, our dedicated team is equipped to handle projects of all sizes.
If you’re unsure about your specific needs or would like to discuss your project with our knowledgeable team members, please don’t hesitate to reach out. In addition to filling out our contact form, you can call us at +86 18123721954 or send an email to long@custompcba.com. We are here to assist you every step of the way.
Get Your Free Quote Today!
Ready to get started? Don’t wait—request your free quote now! If you have detailed information about the PCB services you require, please fill out the additional fields to help us better understand your needs. At CustomPCBA, we are committed to delivering exceptional service and quality products that exceed your expectations.